SurfboardsPrinting A Surfboard From Algae
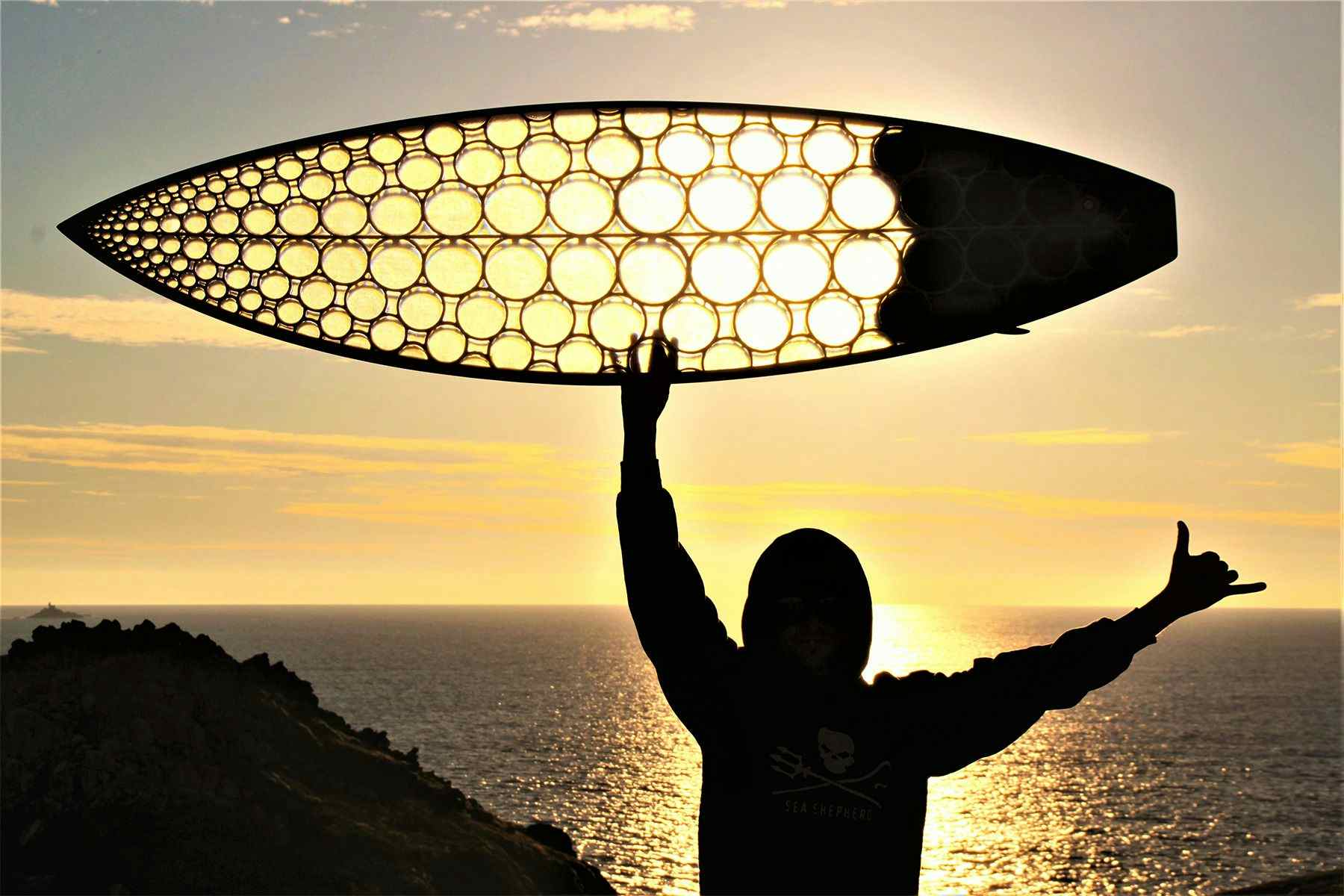
Jérémy Lucas & Paradoxal Surfboards
It is ironic how quickly a blessing can become a curse; how what goes around, comes around.
The range of petroleum-based materials that were considered, back in the 1950s, a technological breakthrough that provided surfers with lighter, more resistant and flexible crafts, have come to represent a threat to the very environment they need to perform their beloved activity. And even though nowadays this paradox is clear, even though the technology, willpower, and creativity to circumvent it are there, the manufacturing methods and materials, as well as their consequences, remain pretty much the same as seventy years ago. And, to a large degree, so does our compliance.
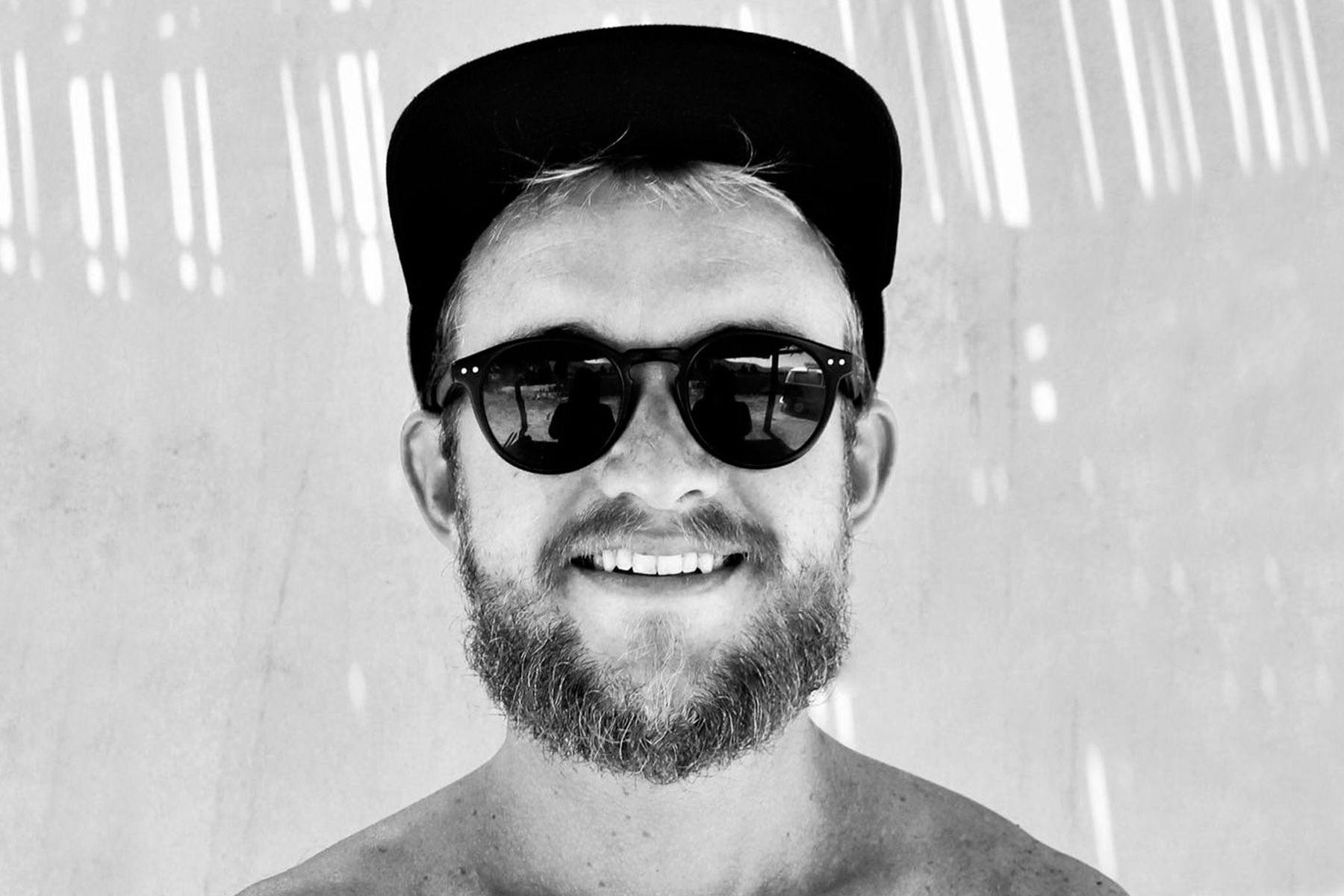
Jérémy Lucas, a surfer-entrepreneur from France, is among the global group thinking outside the box, attempting to turn the tables and make surfing the eco-responsible practice that it can – and should – be. His new project, aptly named Paradoxal Surfboards, uses beached seaweed, a major problem across beaches and surf breaks of his local Brittany, to 3D print surfboards.
“I don’t have an engineering degree, but I have always liked engineering in general,” says Jeremy, who first heard about 3D printing in press articles focused on new technologies. This curiosity led him to start, in 2019, a Mechanical Design studio in Douarnenez, where, together with his partner, they specialised in industrial design (CAD/ DAO) for professionals such as boilermakers and metalworkers, whilst also using their small Ultimaker 2 3D printer to service specific requests from individuals. Eventually, they realised that in order to make the 3D printing business profitable they would need to mass-produce to meet industrial demands – or propose a predefined product with high added value.
“Paradoxal Surfboards is an alloy between my passion for surfing, my region of Brittany, and countless hours of research, exchanges and meetings with many engineers and researchers on the subject of green algae and 3D printing.”
What follows is an email exchange with Jérémy. The text has been translated from French and edited for readability.
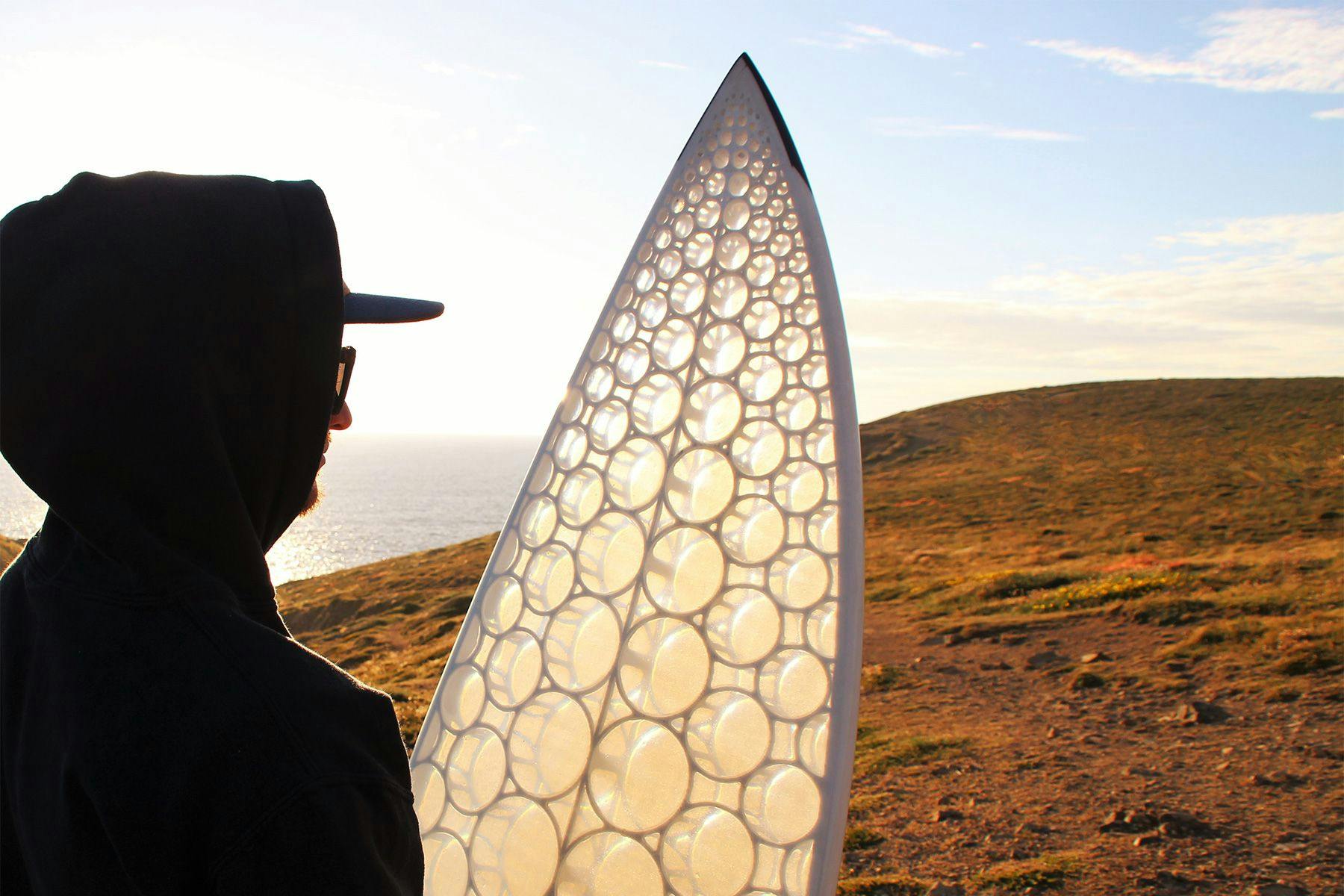
THE ISSUE
The proliferation of green algae is a well-known phenomenon on the coasts of Brittany; it is the result of an intensive and unsustainable agricultural system (nitrates found in fertilisers and waste from pig, dairy, and poultry farms flow into the river system and then the sea) that has been at play for more than half a century. When beached algae decompose, it releases hydrogen sulfide – a threat to the health of living beings, and even though communities often collect the algae with bulldozers – either taking it to treatment centres or using the fumes in the making of biofuel or energy – the problem is yet to be solved.
Figures vary from year to year, and depending on the benchmark between communities and associations for the protection of the coast, but around 30,000 tonnes of seaweed are collected each year on the northwest coast of France. That is 30,000,000 kilos. Considering that we need around 750gr of green algae to 3D print a single surfboard…I’ll let you do the maths on the potential of this waste. [Laughs].
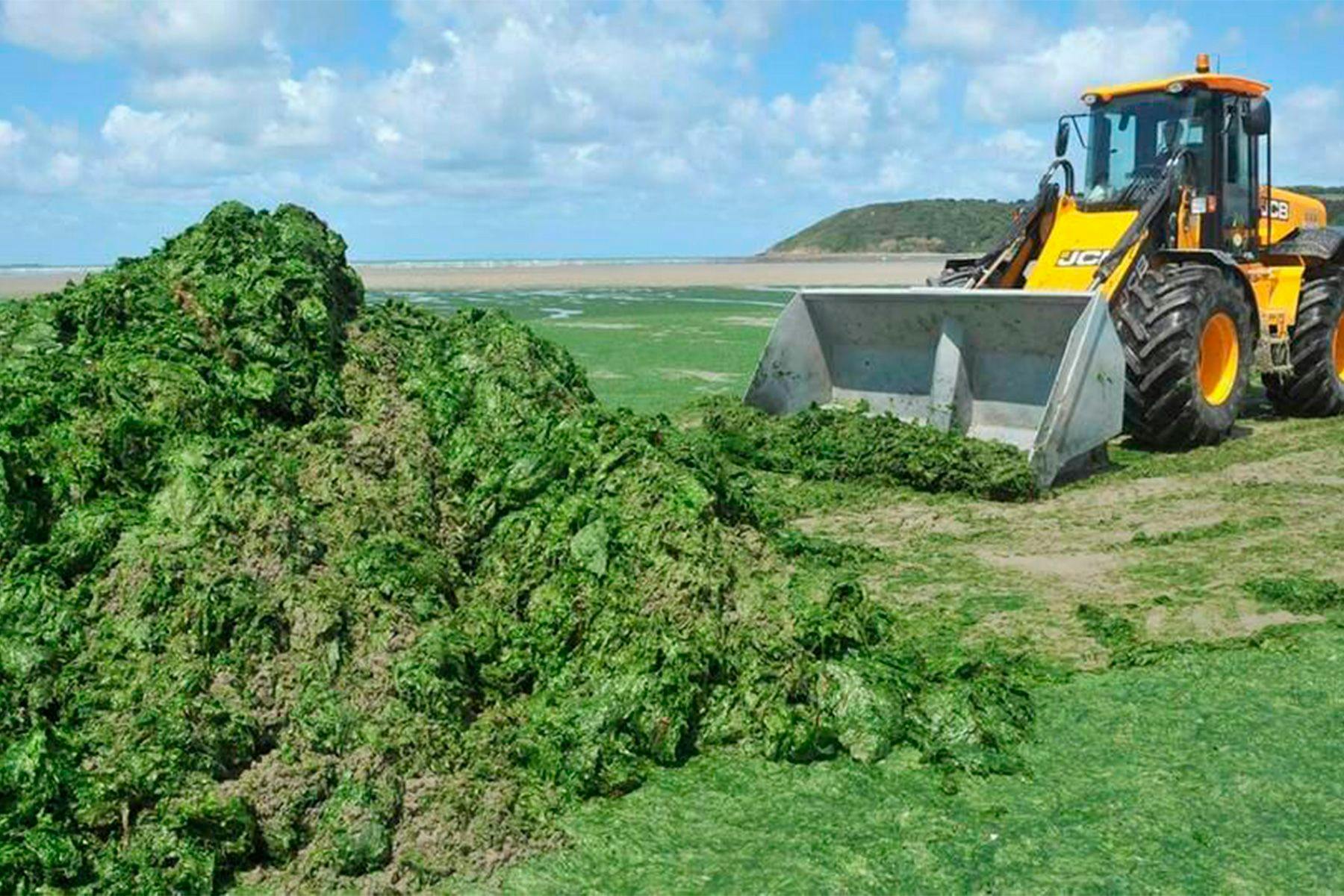
THE IDEA
In December 2019, I went surfing with a few colleagues at Ris beach, in Douarnenez, in the middle of a storm. There was a strong swell, back-wash, the spot was filled with seaweed. I got out of the water in a terrible state – headaches, vomiting, and was bedridden for two days. That’s when it dawned on me that it was time to act, on our scale and by our means, to mitigate this phenomenon of green algae.
A week later, a client asked us about the origin of the materials we used for our 3D prints. We told him that it was mainly a plant-based, petroleum-free plastic PLA (Corn Starch Polylactic Acid). Clearly well-informed, he explained to us that the PLA we used came mainly from the United States and was made from corn sugar, which is very greedy for water, and which, in fact, devastates dedicated biodiversity zones – on top of being a GMO.
Thinking to formulate a new thermoformable material for 3D printing that could be made at home in France, we looked out our office window to the beach and thought – “Why not stranded green algae?” When pondering about what we could 3D print from algae, we quickly made a connection after remembering the surf session of the previous week: “We are going to print 3D surfboards from green algae.”
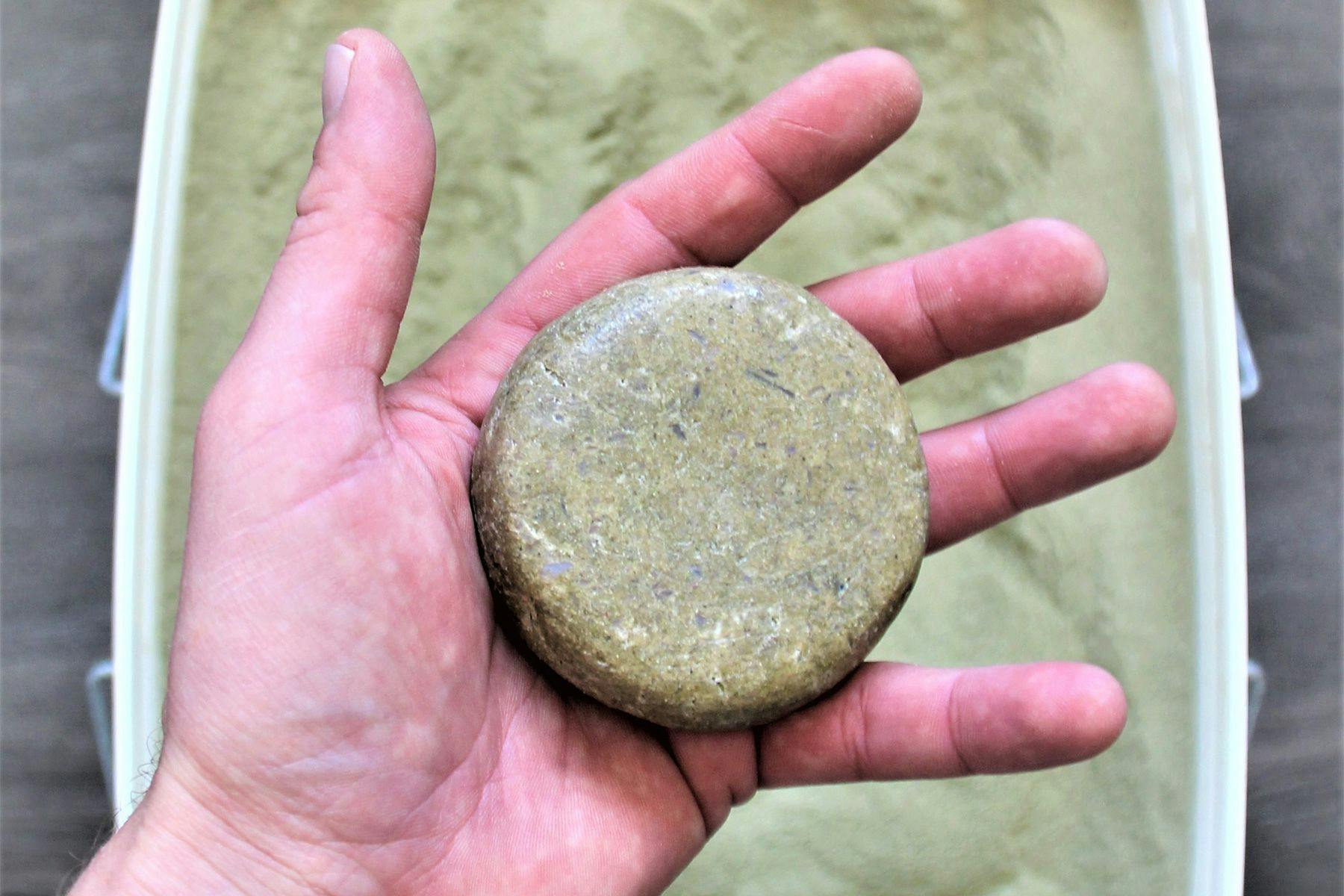
THE PROJECT
We named this project “Paradoxal Surfboards” for several reasons. Firstly, we come to respond to the “surfer’s paradox”. Here’s a person who, by virtue of his sport/lifestyle, consents to a vision that is more respectful of the environment, yet has no other choice than to use (at least some) petro-compound materials (neoprene wetsuits, polystyrene or polyurethane boards, gloves, grip pads, leashes, etc.) which are toxic, non-recyclable, and often travel great distances.
“Paradoxal” also because we aim to revalue, or upcycle, the beached green algae which are, for the most part, considered as waste, and replace the oil commonly used in the traditional manufacture of a PU or EPS surfboard. But more than anything, the purpose of our project is to no longer have a reason to exist. If the green algae stopped proliferating, it would be a fantastic thing for everyone – even for Paradoxal Surfboards. On the day when there is no more green algae, we will be interested in making 3D printed boards with beached plastic, such as fishing nets.
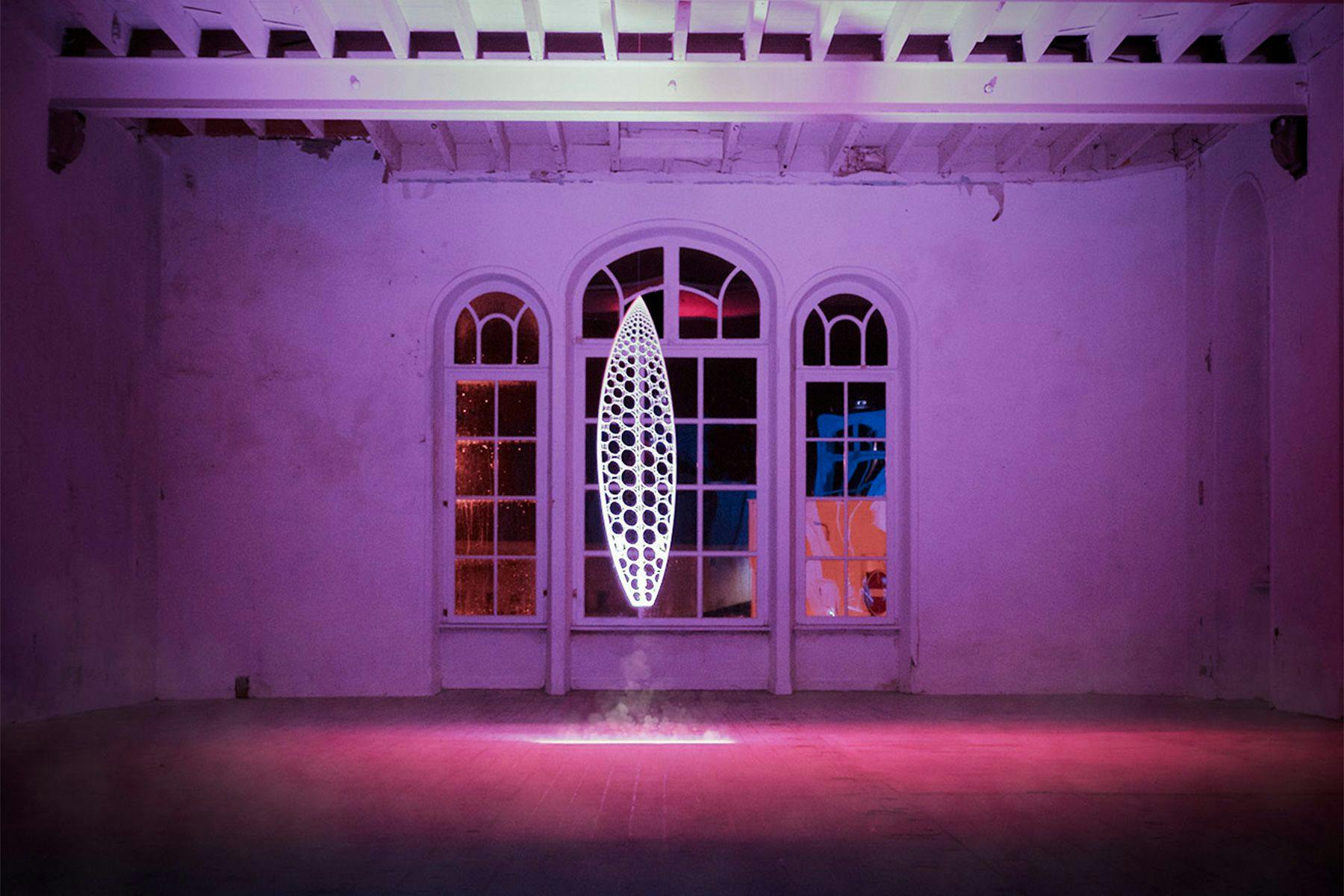
THE METHOD
Once collected, the algae is dehydrated, dried, crushed, and then you can do whatever you want with it: animal meal, compost-fertilizer or, in our case, a thermoformable material for 3D printing. The blueprint of the surfboard itself is simple, but relatively complex to put in place since it involves a certain multi-skill. To make these surfboards we needed three things:
Industrial Drawing – CAD / DAO:
Starting from a blank page and 3D drawing, a 3D printable surfboard is no easy task. We had to strike a balance between a relatively innovative design that uses the right amount of printable material for a production cost that also fits within a certain time frame – after all, the economic model depends on it. All the while taking into account the performance of the board, its final weight and load distribution, and the post-production.
3D Printing:
Once drawn, the board must be printed with the appropriate material in a large volume 3D printer. Although currently time-consuming, 3D printing remains an energy-efficient technology; it allows the realization of complex design structures that are almost unachievable by a craftsman in a conventional way. In addition, 3D printing allows the use of a wide variety of materials with different properties.
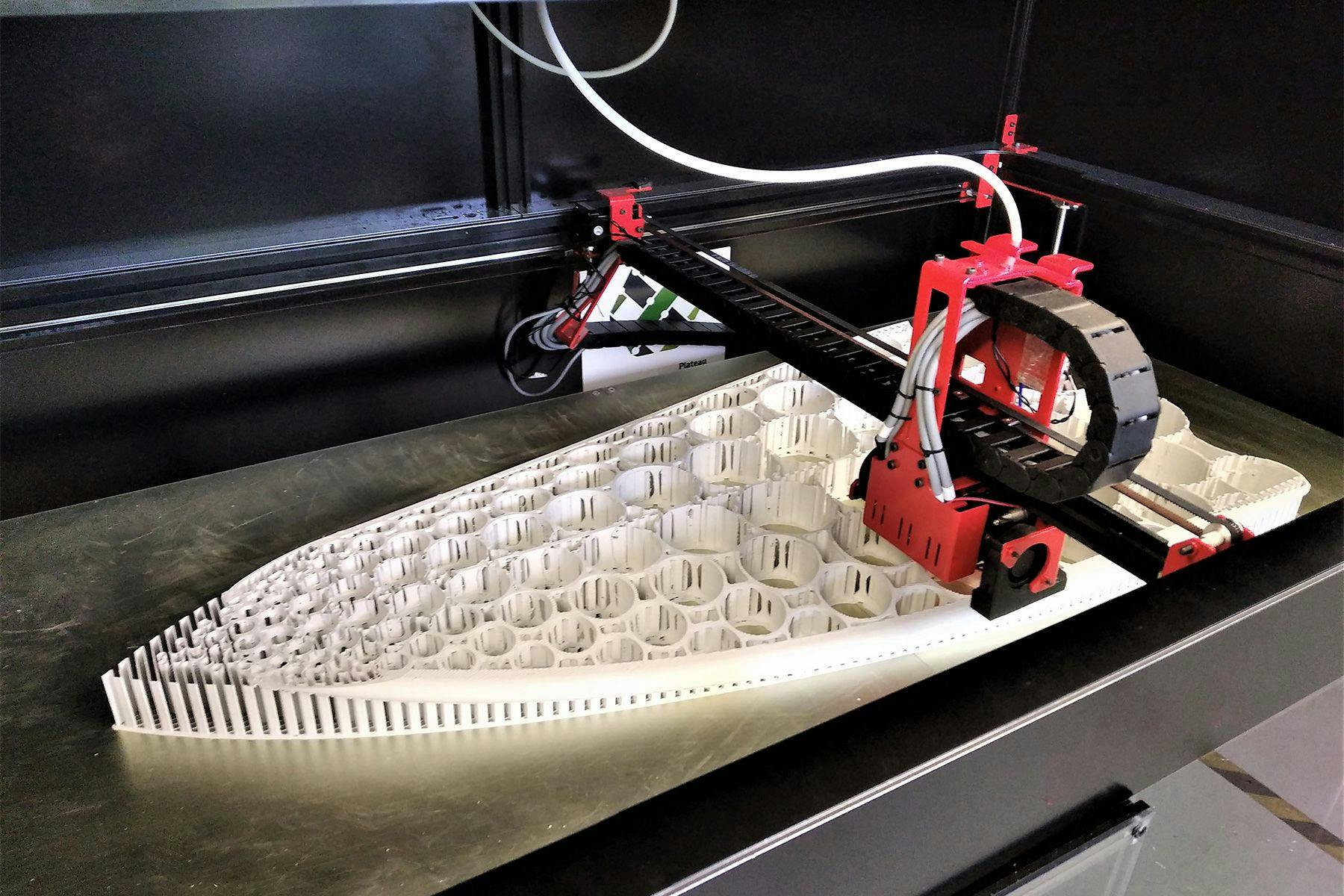
On this prototype, the core of the board (which replaces the foam blanks traditionally used) is printed in two parts which will subsequently be heat-sealed. Print settings are complex to set up and require some iteration before obtaining a top-performing end product. On this first model, we were inspired by bio-mimicry – the structure of a green alga to be more precise – as explained by Idriss Aberkane.
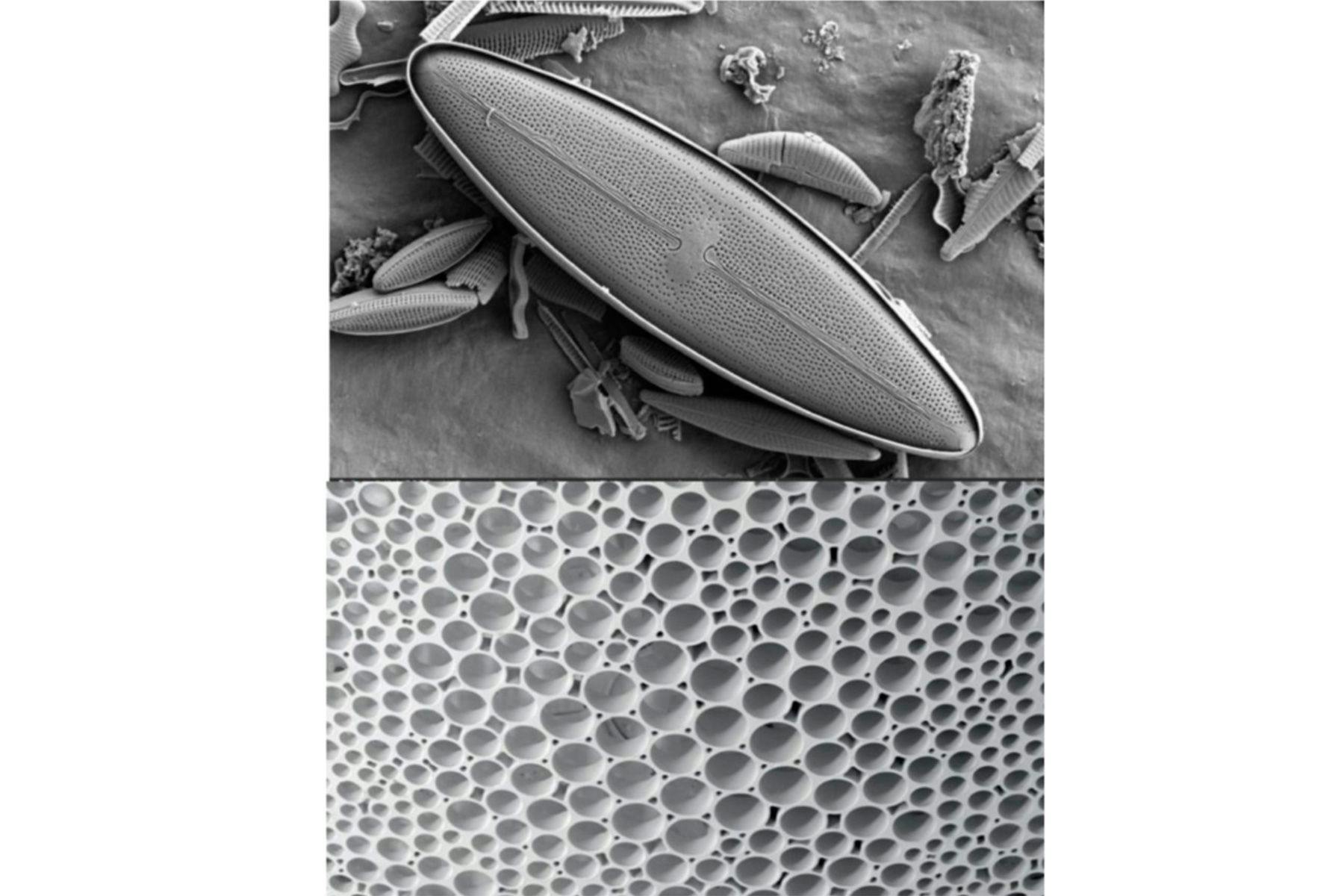
The above is a nanoscale view of a diatom (bottom photo), which is a green alga found all over the world. Since the purpose of our project is to 3D print surfboards from beached green algae, we thought it made sense to base the design of the internal structure on the very organisms we were using. After the nanometric scale, we looked at the microscopic scale of this same alga (top photo). To our surprise, it looked oddly like the shape of a surfboard!
3D printing also makes it possible to print the equipment associated with the board. For example, we 3D printed the core of the surf fins from corn starch and then laminated them with recycled carbon from offshore racing boats, such as those used in the Vendée Globe.
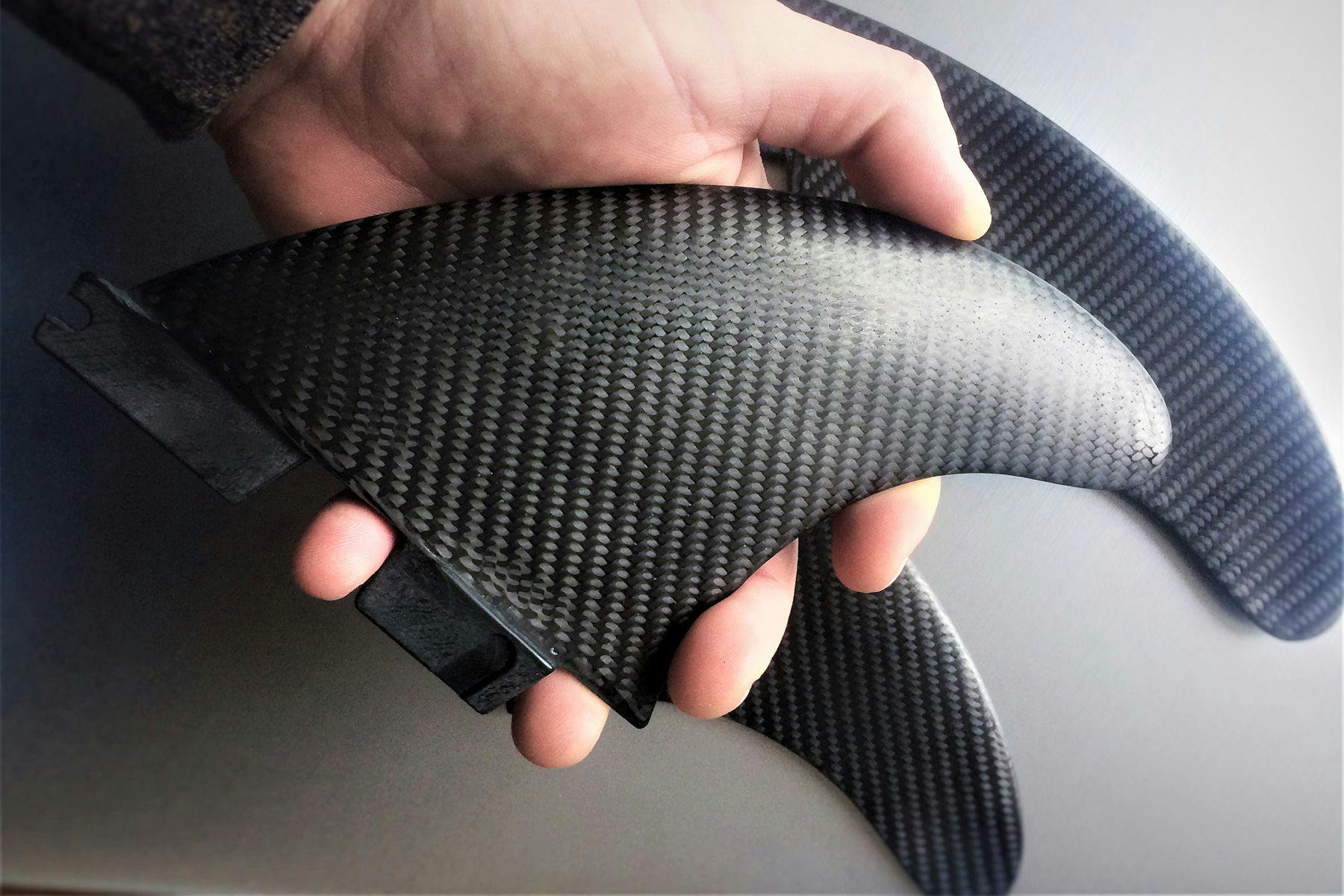
Laminating/Glassing:
Once the internal structure has been printed, the board must be sealed by covering it with fibre and then impregnating it with a resin. This is the laminating/glassing stage. For this first model, which had fairly large, alveolar structural cells, the range of the fibre was a problem. Therefore, we opted for a “reverse lamination process”: making moulds in the negative shape of the board so that the fibre matches the structure and we’re able to laminate it. The calculation of the fibre range was difficult to predict, and this relatively complex step was the result of a great collaboration with several engineers and technicians specializing in composite materials in Brittany. Thanks to the “poached” method put in place by François Gabart’s team at MerConcept, we have an impeccable rendering.
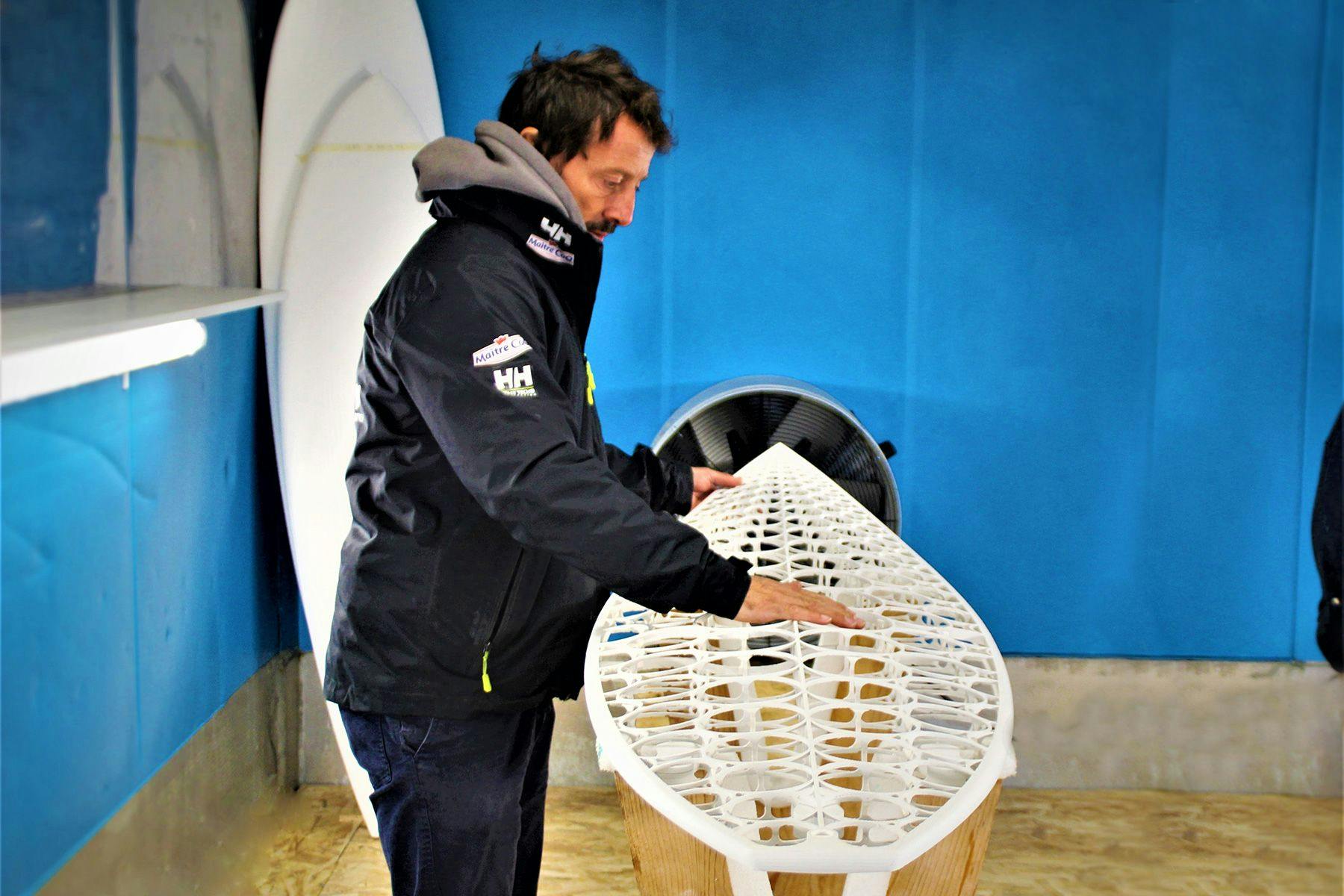
THE SURFBOARD
If there is one important thing in this project, it is the performance and durability of the boards. The ecological side is hardly a selling point anymore, but an essential. The idea is not to eco-produce boards that don’t last over time. If the renewal rate of these boards is lower than that of a traditional polystyrene board, then we’re all wrong!
Thinking of the performance, we approached the best shapers in the area to refine our calculations. We got a 6.0 board with 30L and a weight of 3.4kg. Although predictions in hydrodynamics, fluid mechanics, RDM (Material Resistance) calculations have been made on a computer, it is only how the surfer feels in real conditions that can be the judge. This first board was a real success on several points – but also has some flaws that need to be corrected on the next iteration. For example, it feels a little too stiff, and the central structure will have to be modified to ensure longer lifespan. In terms of production costs, we are really satisfied.
In the specifications for the thermo-formable material, we had the choice of making it a recyclable or biodegradable material – we chose the first. If the board is broken or cannot be repaired, it can be brought back to our workshops, subject to a discount on the next material, so we can pass the core of the board (the one that is 3D printed) through a crusher and then an extruder, thus remaking the reel of material. Also, although fibreglass was chosen on this first model, we are considering applying flax or hemp fibre for future boards.
Also, there is a specificity about this kind of board: Due to their internal vacuum structure, we installed a Goretex type pressure relief valve at the leash attachment. In order to release the pressure stored during the session, as well as with temperature variations, the surfer must open and leave this valve open after each session, closing it before returning to the water.
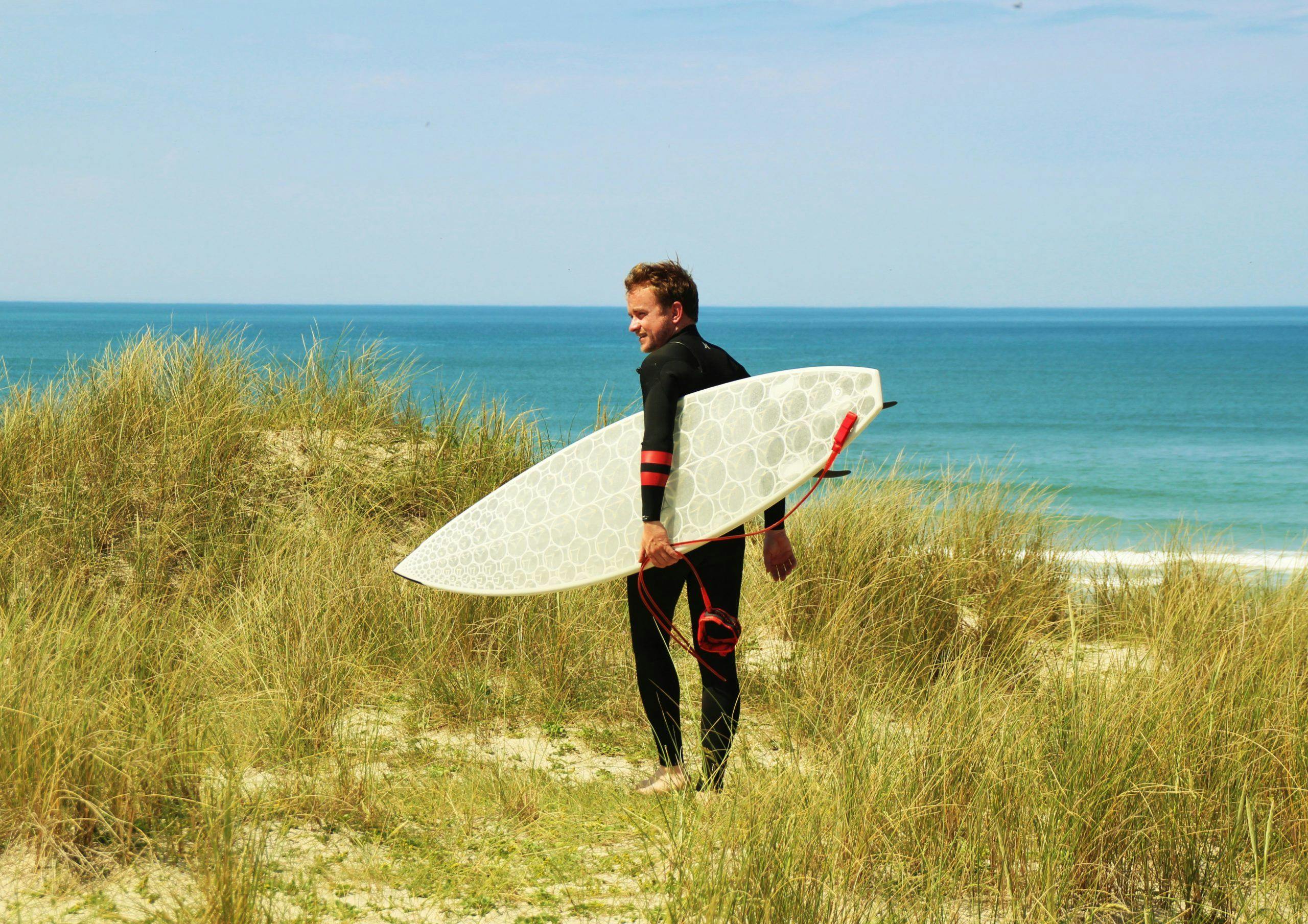
THE FUTURE
I think that, in terms of designing and manufacturing, the “eco-design” side will come to occupy a the predominant place in the world of surf hardware. On one hand, the use of new materials is a very promising avenue to explore, and if I had to choose, I would like to experiment with gull droppings, which is also a plague in Brittany! [Laughs]. But so are new manufacturing methods. 3D printing is under-exploited nowadays in this sector – the potential is enormous. And there is surely something to be done with 4D printing.
Moreover, we can bet on the use of “intelligent” materials that interact with their environment, depending on temperature, pressure, exposure to light, etc. or that provide information on the quality of the water or the surrounding fauna of the local ecosystem of the surf spot. There is also already work being done on Shape Memory Materials (SMMs). For instance, if the board presents a deformation following an impact, the fibre would return itself to its initial shape in correction. This already exists to prevent potholes on the roads with shape memory concrete – so why not with a fibre intended for surfing?
Paradoxal Surfboards was, until last March, an intrapreneurial project led by a young Douarnenist start-up that I co-directed and which, unfortunately, no longer exists. The project is therefore suddenly slowing down and my biggest challenge is probably to give it a “follow-up” as a single project leader and no longer as a company. There’s also work to be done in refining this new thermoformable material
*****
The author would like to thanks Jérémy Lucas for his assistance in the article. To find out more about Paradoxal Surfboards visit their Facebook page or follow them on Instagram.