technologyFins For All
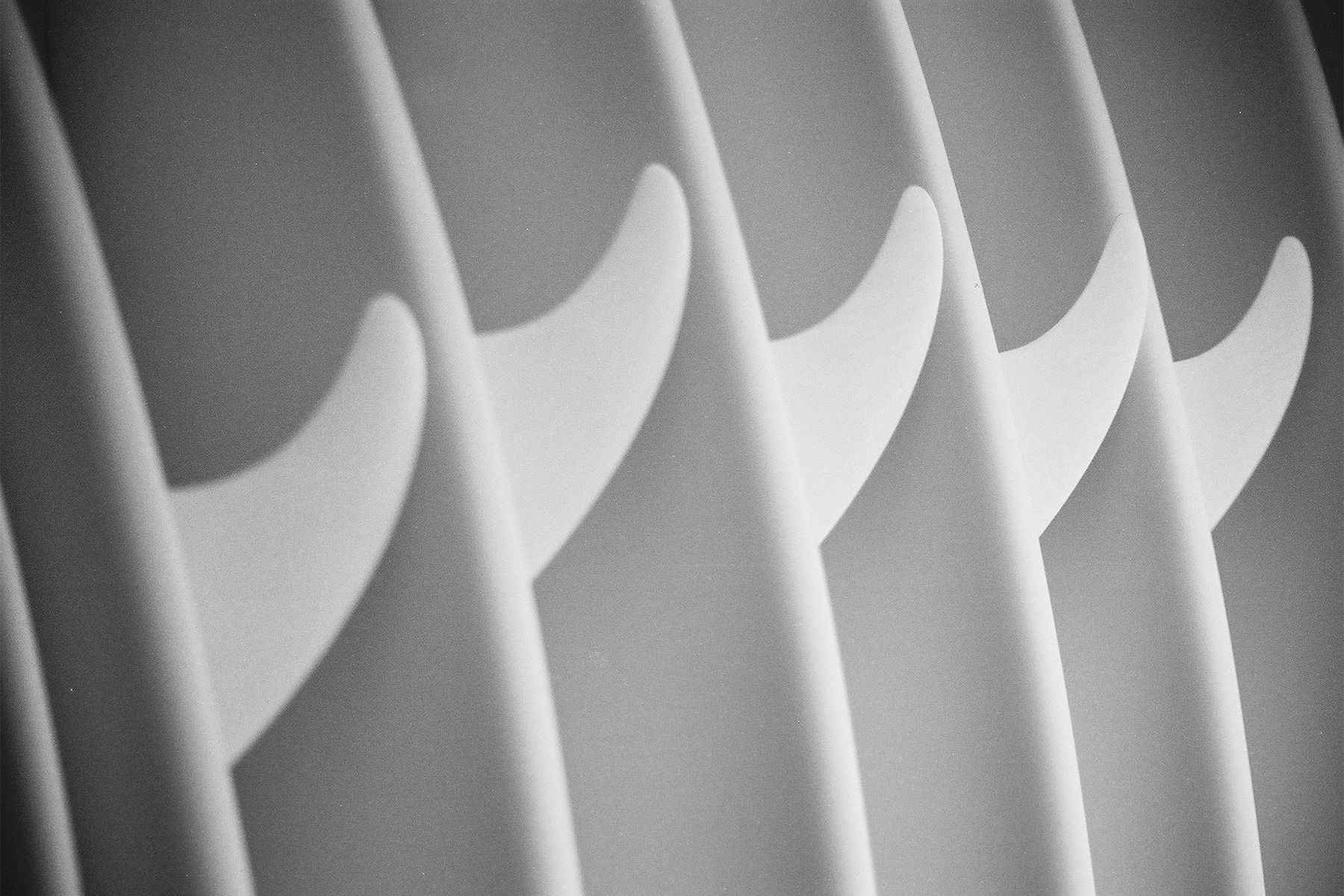
A Parametric Method For 3D Printing Surfboard Fins
Dr James Novak grew up hundreds of kilometres away from the ocean in country New South Wales, Australia. He made his breakthrough into 3D printing by designing the world’s first 3D printed bicycle, and currently applies his expertise into neurosurgery and maxillofacial surgery as a senior research fellow for the Craniofacial program at the Herston Biofabrication Institute (HBI). He is perhaps not the most obvious candidate for undertaking innovative research into 3D printed surf fins, but that is exactly what Dr Novak has done. In his paper, James, an award-winning designer who came to surfing through kitesurfing and windsurfing, aimed to solve one of the biggest dilemmas when it comes to 3D printing surf fins: that despite the extensive body of research on materials, technologies, and performance, designing a surf fin for 3D printing remains the remit of those who know their way around computer-aided design (CAD). For that, James created an interactive, parametric system that allows those with no previous CAD knowledge to customise the geometry of their own fins in real-time, making them ready for 3D printing by simply adjusting fin properties (such as fin system, position, cant, depth, sweep, base length, etc.) through a series of sliders and dropdown menus in a custom design app.
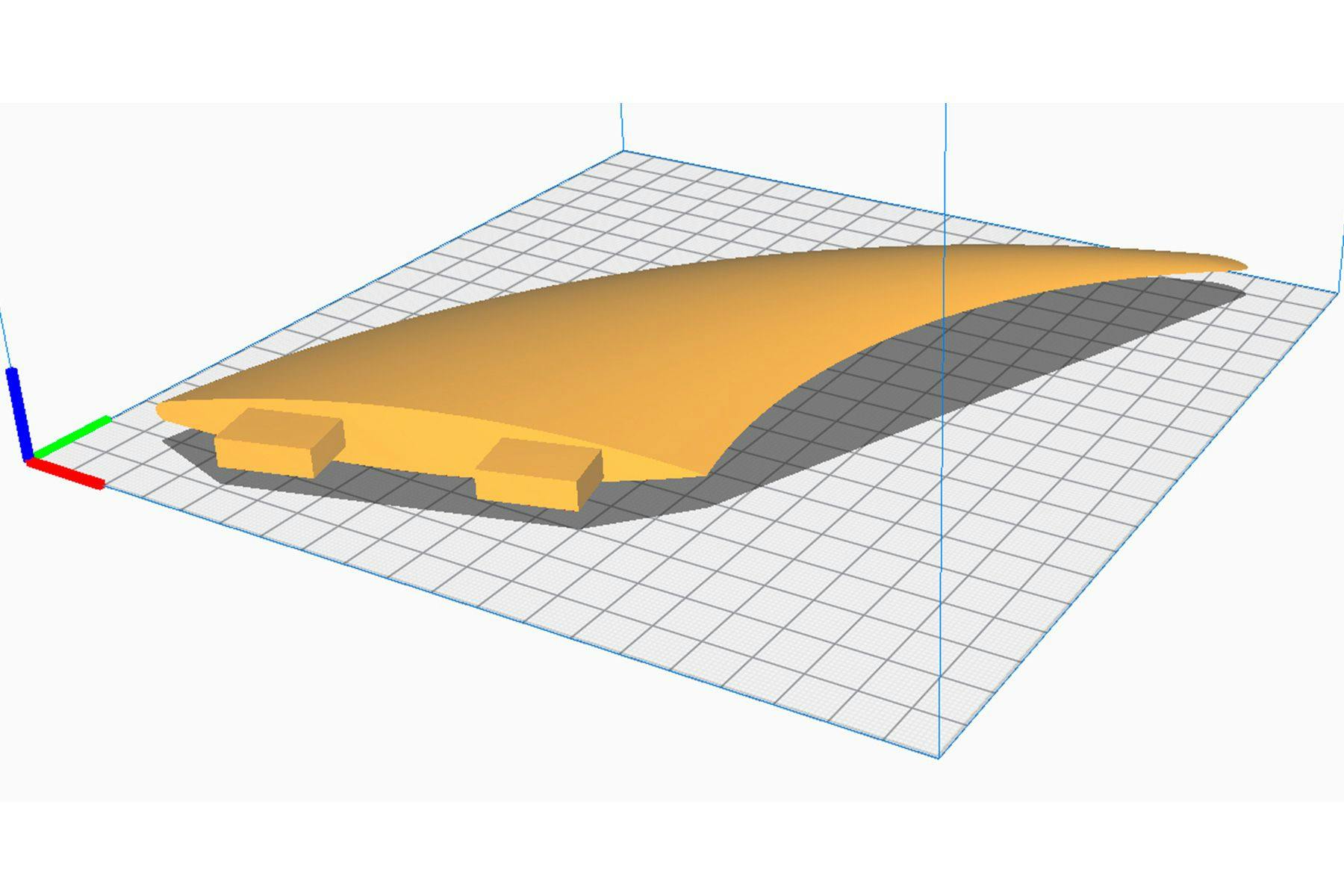
Surf Simply caught up with James to learn more about the motives and motivations behind the research, the pros & cons of 3D printing surf fins, and his take on the future of this technology.
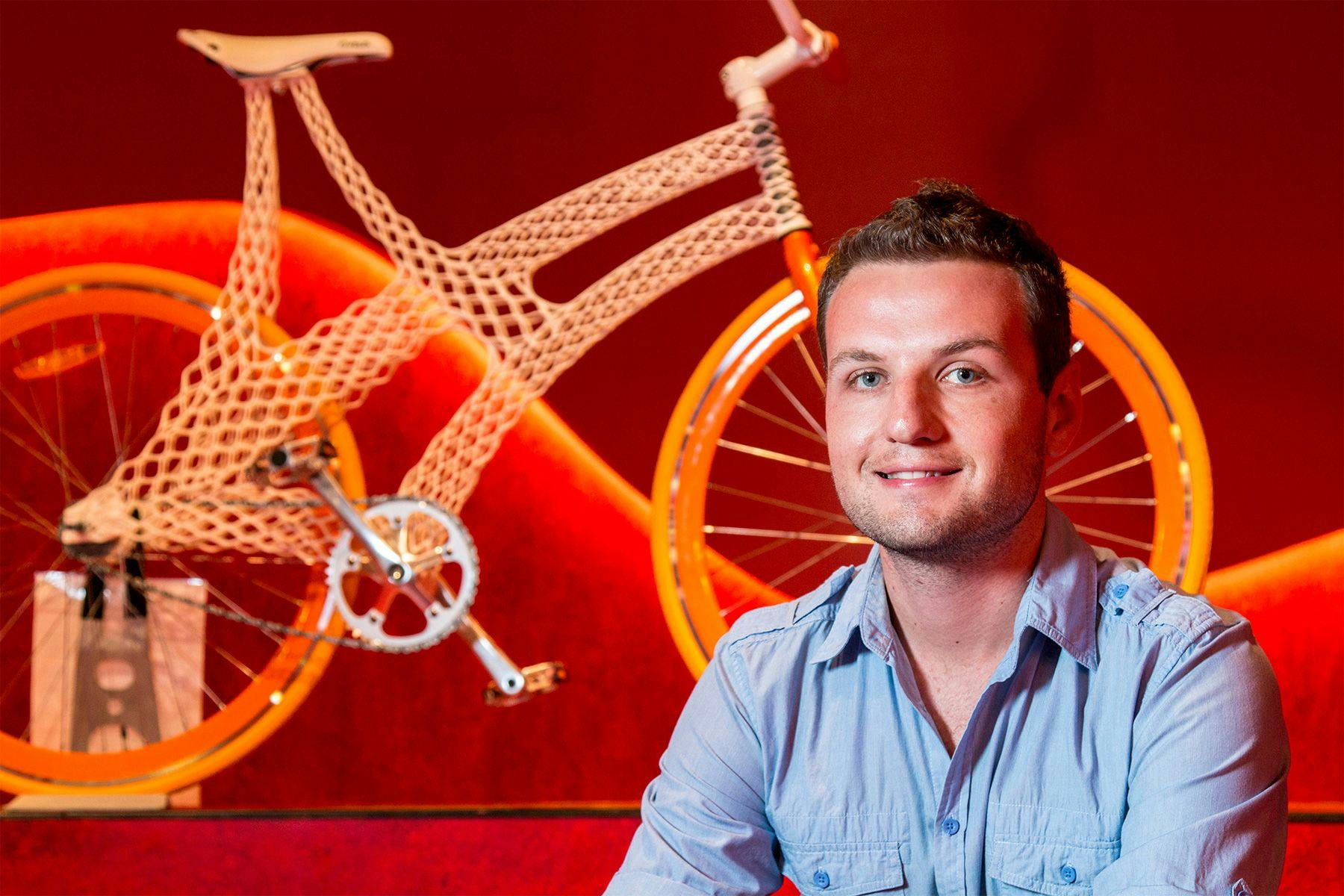
James, what is it about 3D printing that interests you?
I’ll start out by saying that I’m a bit of a 3D printing geek! For a designer like me there is something quite amazing about starting with nothing more than an idea, and within a matter of hours, having a physical 3D printed product in your hands. This ability to rapidly test ideas and iterate is one of the things I enjoy most about the technology, as well as the way it allows designers to fabricate complex geometry that was never previously possible. There are always new types of 3D printing technology being developed, as well as new materials and applications, so it’s a really exciting and fast-paced field to be involved with.
Where did the idea for the research on surf fins come from?
I’ve been using 3D printers since 2009, and have had one or more 3D printers at home since about 2014. So, combining 3D printing with one of my hobbies, kitesurfing, was a very logical fit, and an early project I began in 2014 – it was actually the very first post on my 3D printing blog! I was curious about the strength of 3D printed kiteboard fins, as well as the ability to change the geometry and what effect this could have on my performance. At the same time, I was completing my PhD at Griffith University, focused on technologies like 3D printing, so as a student the opportunity to 3D print my fins for a fraction of the cost of buying them was very appealing!
The research that I recently published into 3D printed surfboard and stand up paddleboard fins came much later and was a bit of a cheeky way to combine my work (at the time I was a postdoctoral research fellow specialising in 3D printing at Deakin University) with play. I had been following a lot of the great research into 3D printed surfboard fins coming out of the University of Wollongong, but noticed that there were no simple tools for people to design or modify surf fins for 3D printing, unless they had several years of training in advanced computer-aided design (CAD) software like me. I wanted to explore advanced software tools that would allow just about anyone without CAD expertise to design and modify surf fins with just a few simple tools. This way, anyone with access to a 3D printer could enjoy the sort of experimenting I had been doing over the last few years.
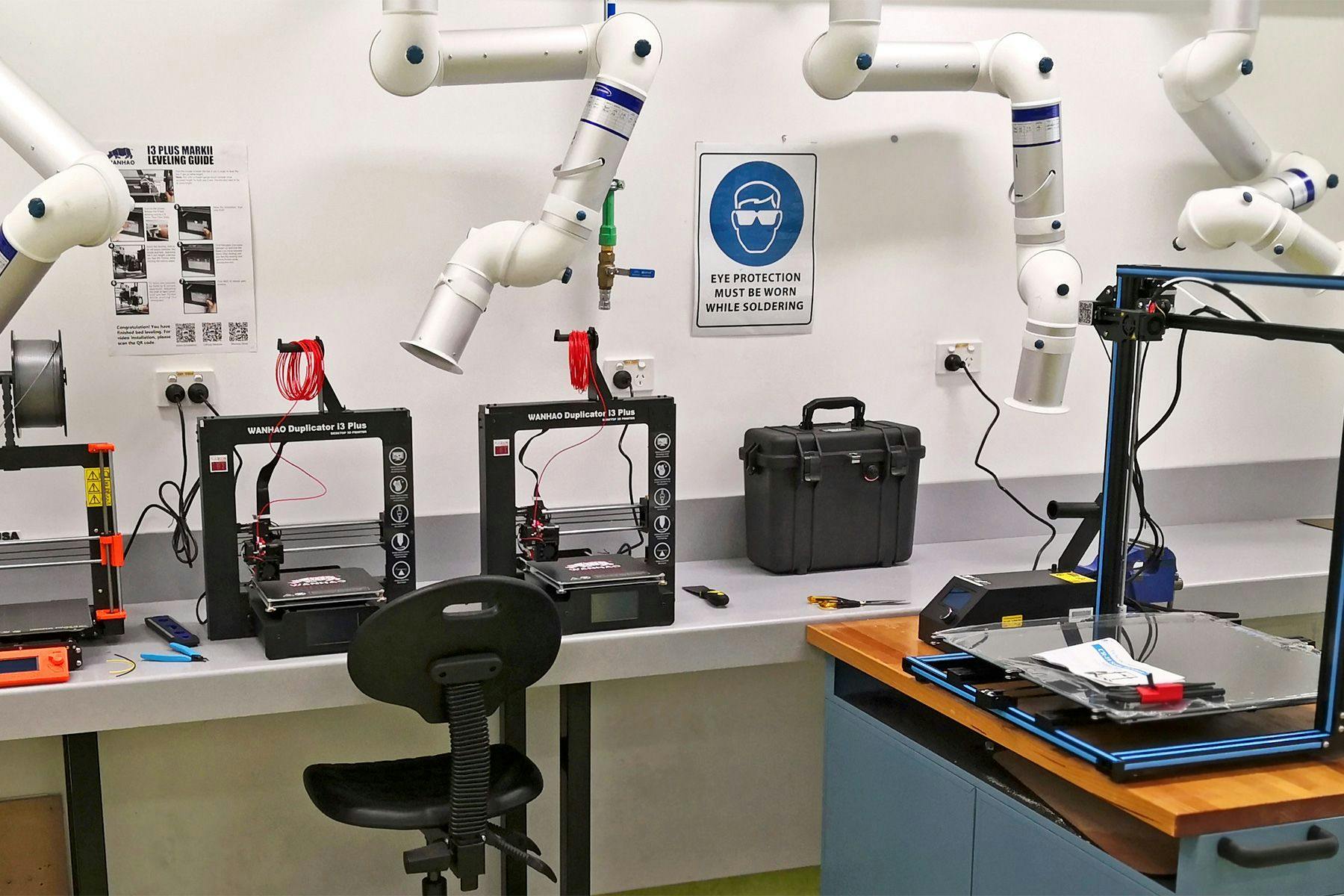
Can you please talk a bit about the behind the scenes of this research, particularly the hands-on side of it? What did a day in the lab look like, for example?
The main lab where I was working at Deakin University was a makerspace we set up for research and experimentation with a group of like-minded researchers (pictured above). We all brought our own machines to the space, so could experiment with different modifications, materials and ideas away from the main 3D printing facilities of the School of Engineering. Most of our machines cost $1500 or less, so nothing fancy, but very effective for hands-on research and testing. And because of the low cost, you can take some risks that you are less likely to do on 3D printers costing tens- or hundreds-of-thousands of dollars. I think this hands-on learning with 3D printers is critical to understanding the process and how to design for it.
Once you have a solid idea, then you might go and 3D print using more advanced processes and materials, which we had available at the university, or that can be outsourced to 3D printing service bureaus. One of the surf fins I 3D printed and was pictured in the published research was outsourced to a service bureau overseas so that I could get the material qualities and smooth surface finish I wanted (pictured below).
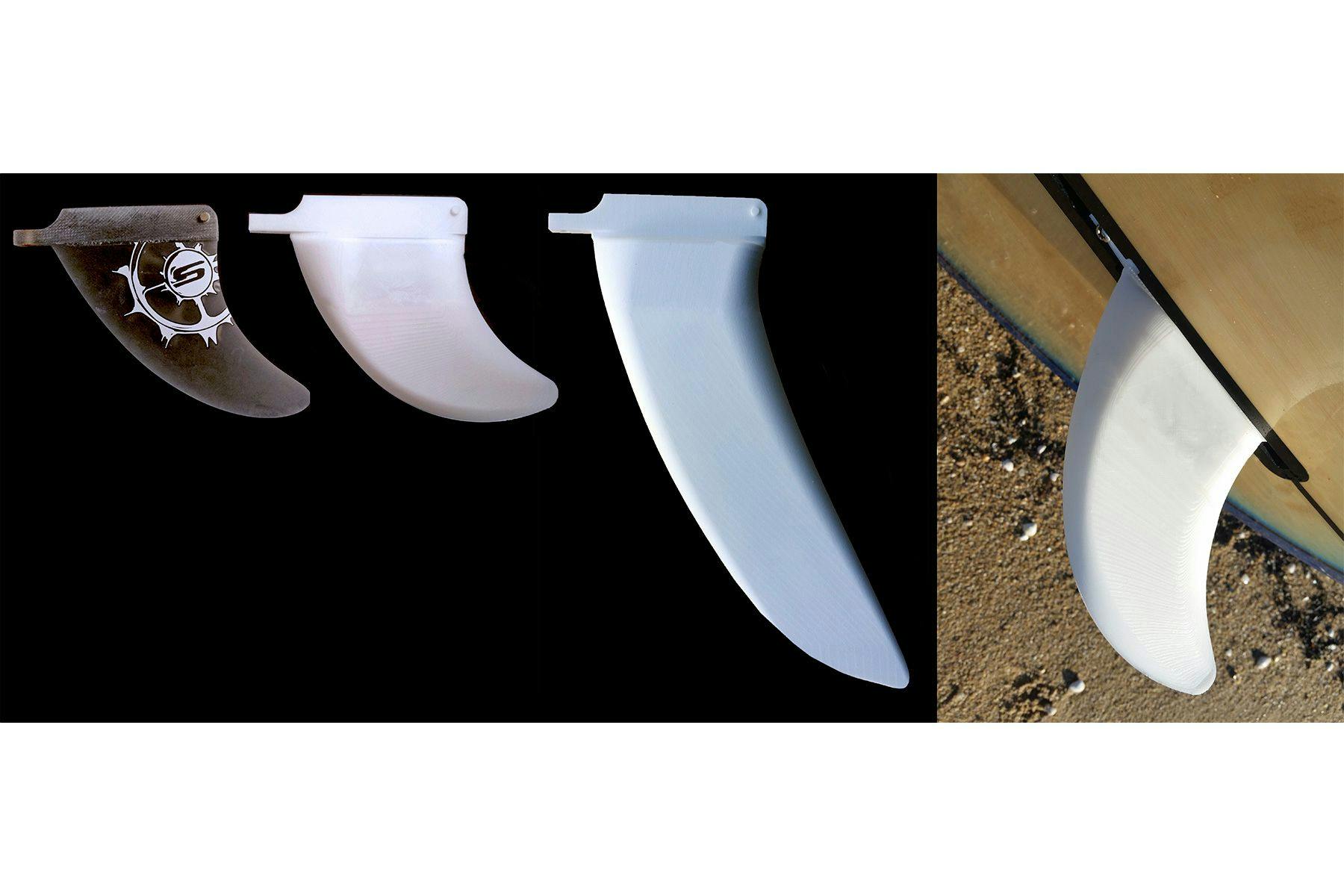
In the blog you’ve been running since 2014, you share a lot of information about your projects and research, big or small, including free downloads of designs you’ve worked on. Based on your experience so far, what would you say are the benefits of documenting the process behind the stuff you make? And in the ever-growing – and I suppose increasingly competitive – world of 3D printing, why share knowledge for free?
Great question. As a professional designer and researcher, a lot of my work is published in academic journals most people never read, or is tied up with intellectual property (IP) and commercial agreements. This is fine, I love what I do and have been able to make a career out of 3D printing. However, as a 3D printing geek, there are a lot of designs that are just a bit of fun or a personal project, and I get a lot of satisfaction and enjoyment from seeing others get to use these. So whenever I can, I share what I create.
This sharing mentality is actually an important part of 3D printing culture – the early RepRap desktop 3D printers (short for replicating rapid prototype) were actually released as open source plans and files for anyone to use in the mid 2000’s, and this mentality has continued as the technology has matured. Many of today’s most popular 3D printers are still based on these early designs. I’m constantly learning from others in the 3D printing community, and I think it’s important to give back whenever I can. This includes documenting designs and projects on my blog so that others can learn from my successes and failures, or learn how to design different geometries using different software, or just a place to find some of my free files that people can download. Even better, I love seeing people modify and adapt my designs – for example, one kitesurfer modified my kiteboard fin design to act as a stabiliser for his foil, while someone else just changed a few dimensions to accommodate different screws. Because 3D printing files are just digital data, like a song or video, it’s incredibly easy to share and modify designs.
In the introduction of the paper you highlight how, despite the many manufacturing methods for producing surf fins, they all have to either compromise on cost, or the complexity of the process, or on the range of geometries available – which is where the potential of Additive Manufacturing lies. Could you please share your thoughts on the present and future of these standard methods and technologies, as well as the current issues of mass-produced sports equipment, particularly surf equipment?
A lot of people ask me whether additive manufacturing is going to replace traditional mass production technologies, and the short answer is No. It is just another way to make things that is cost-effective in some scenarios, and not others. What we are seeing in many industries is that there is room for mass production AND additive manufacturing technologies to co-exist and address different market needs. For example, it makes no sense for a manufacturer to suddenly decide to 3D print all of their surf fins if those surf fins are exactly the same size and shape for every customer. Technologies like injection moulding make it very cheap to produce lots and lots of the same product, and they can do it in just a few seconds. 3D printing a single surf fin can take several hours! However, because of the high initial setup costs for injection moulding (i.e. making metal tooling), it wouldn’t make sense to use this manufacturing method if you only needed a few fins in a certain shape, and would never make them again. This is where additive manufacturing has an advantage as it is cost-effective to produce low volumes of unique parts, even just a single surf fin.
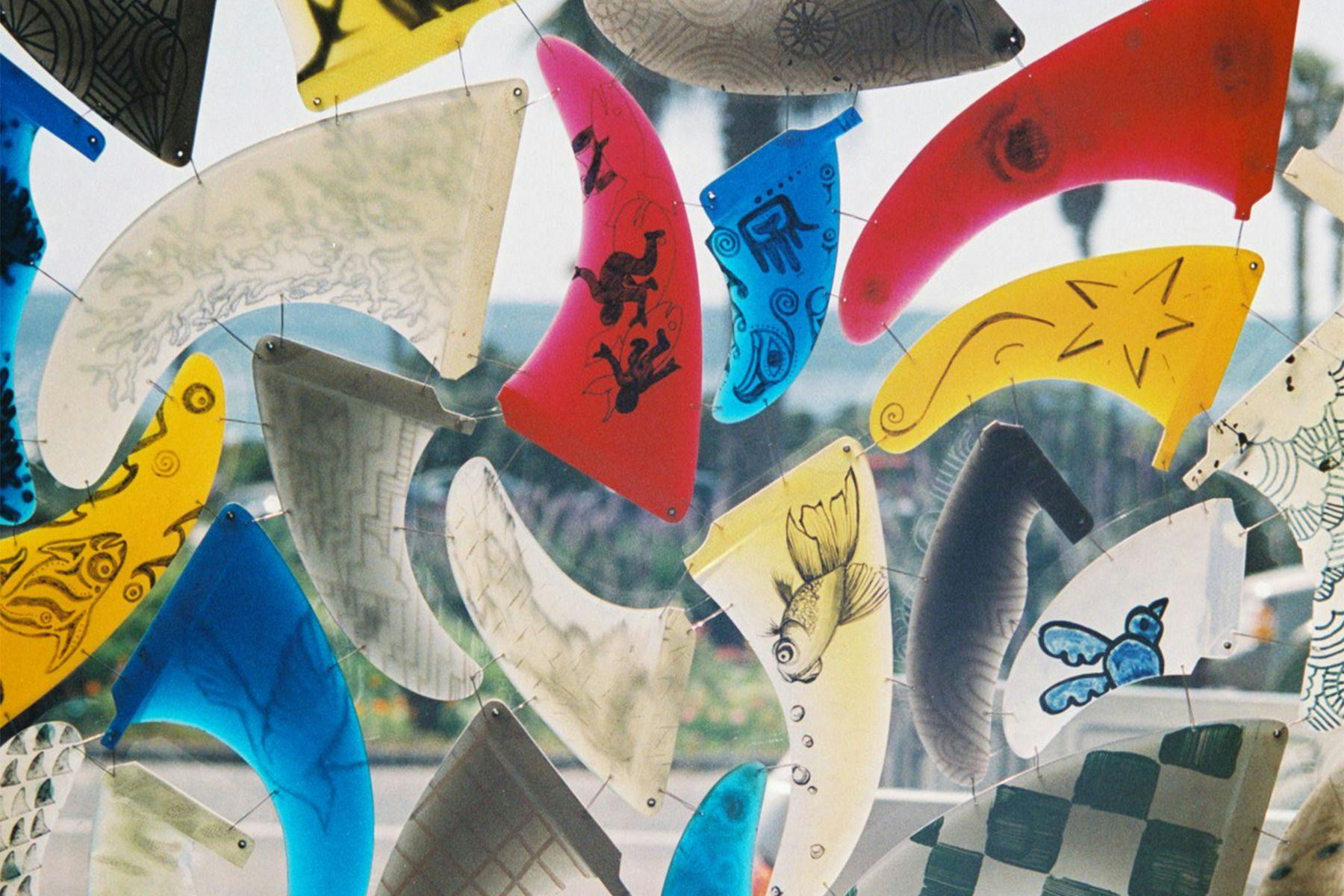
Where additive manufacturing is finding value in the sports industry is creating unique equipment that is perfectly fitted to an athlete, or performs in a way that optimises a particular athlete’s performance. Elite athletes have always had specialty equipment made for them to do this, but now additive manufacturing provides a new and more accurate way to fabricate products compared to handmade, and can be seen in just about every sport from cycling (bicycle frames, handlebars, cranks, helmets) and running (shoes), through to Paralympic sports and of course, surfing! 3D printers are widely accessible and are going to continue to be used to help both elite athletes, as well as recreational athletes who can now have a 3D printer at home for cheaper than a gaming console or computer.
The purpose of this paper was to detail a parametric CAD design that would allow surfers with no CAD experience to effectively customise their own fins. At some point, you also mention the “capacity for 3D printing to empower ‘prosumers’, a term used to describe people who both produce and consume products, bypassing traditional supply chains.” I’m wondering if you could comment on the potentials and challenges of 3D printed fins to find their place (or build their own?) in the existing surf fin market?
I think the commercial opportunity for 3D printed surf fins is yet to be realised, not so much because of any technology limitations, but because surf fins are already available in quite a large range of sizes and shapes. Most people can probably find a fin that will give them the performance they want in most conditions, and don’t have the time or interest to make minor tweaks and modifications. So I do see this as a tough market compared to other sports equipment that may more closely interact with the human body, like helmets or gloves, which are perfect for 3D printing’s ability to produce one-off products that may be designed from a 3D scan, for example.
The “prosumer” market is definitely one area where 3D printed fins will continue to grow – those people, like me, who have a 3D printer, or can access one, and will become manufacturers of their own equipment. This is not likely to be a large market because of the skills and time required to design and 3D print fins, but it is going to be innovative. It may even see some entrepreneurial minds create niche businesses 3D printing surf fins.
There is always going to be a cool factor to 3D printed surf fins, and this is a potential marketing tool that will help businesses carve out a space for themselves. However, it could be a novelty that wares off. New materials and combinations of materials will definitely help create new opportunities for surf fins, whether that’s biodegradable polymers that are better for our oceans when fins break off, or new combinations of materials that create different performance properties that can’t be replicated with other manufacturing methods. The layer-by-layer nature of the technology means complex internal geometries are possible, as is the opportunity to lay up different combinations of materials as you go.
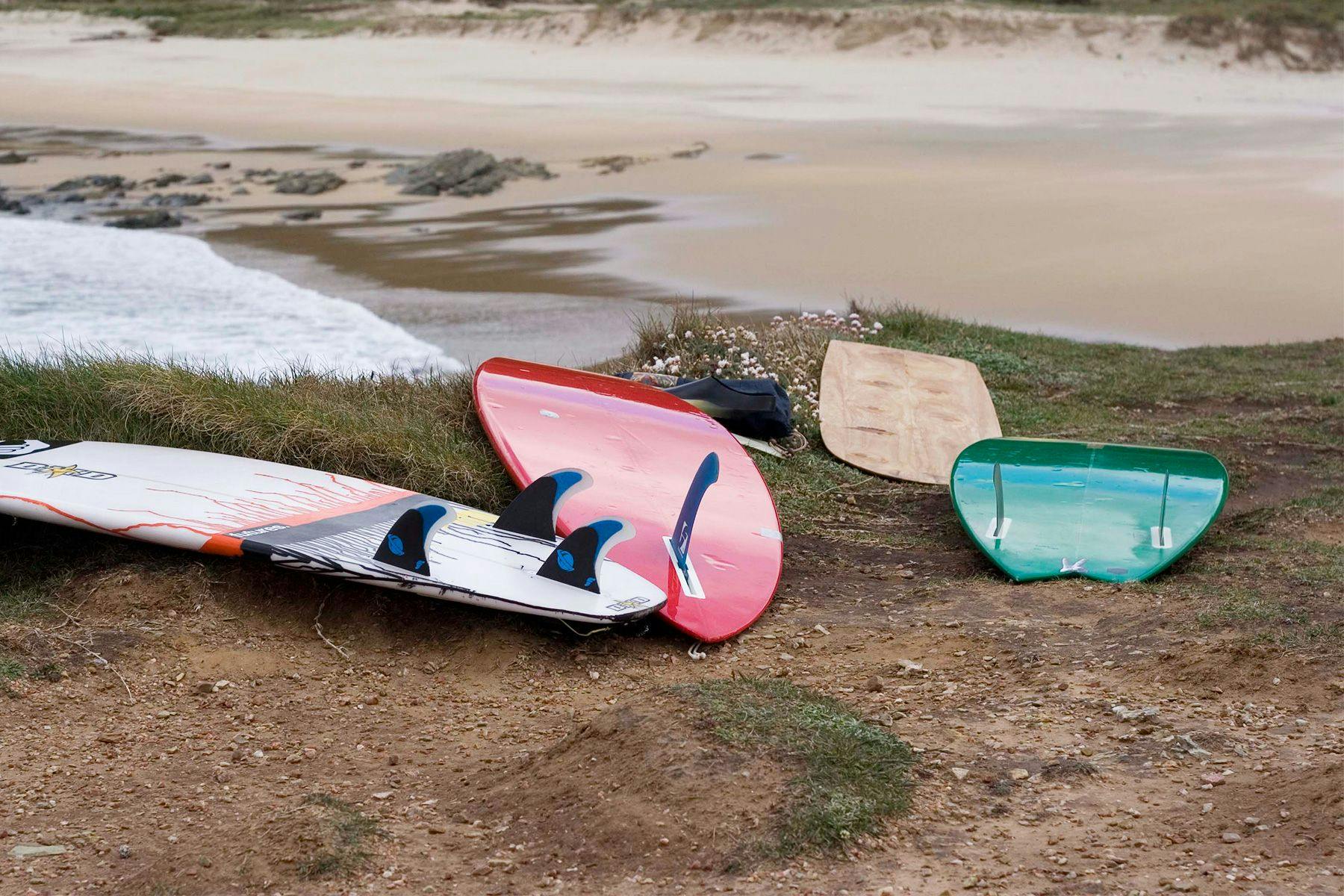
When it comes to surfboards and surfboard fins, what are some of the downsides of Additive Manufacturing – both financial, logistical, and environmental?
Some of the disadvantages have been discussed previously – 3D printing is a slow process and not suited to making large numbers of the same product. Financially, this may mean that a 3D printed surf fin or surfboard (if sold in a store) will be more expensive than a comparable mass-produced surf fin or surfboard. However, compared to a custom-made fin or board, a 3D printed version might be quite competitive. If 3D printed at home on someone’s personal 3D printer, the cost might be very low, but maintaining quality and having reliable mechanical performance is also much harder than traditional manufacturing methods. Desktop 3D printers can be very unreliable. And we are unlikely to ever see many people own a 3D printer at home large enough to print an entire surfboard!
Another disadvantage of 3D printing is that it can encourage a lot of plastic waste – in the process of experimenting with lots of different fins, what happens to all the designs that don’t work? Most of the plastics people 3D print with are technically recyclable, but you can’t just put them in your recycling bin because they don’t have the appropriate identification marks. You can also print with biodegradable plastics, PLA (polylactic acid) being the most popular, derived from corn starch. However, it only degrades in very specific conditions, so still typically ends up being a waste product.
Logistically I don’t think there are any downsides, only upsides for additive manufacturing.
Speaking of plastic waste. I was wondering if you could expound on the potentials of additive manufacturing vs standard mass-production in minimising environmental impact? Are there ways to make additive manufacturing less environmental impactful?
3D printing does hold a lot of potential to reduce waste – because you typically only 3D print the products you need, when you need them, you don’t end up manufacturing thousands of the same product (mass production) that might never sell. It is quite common for mass produced goods to end up in landfill once they are no longer useful, or if they simply don’t sell in the volumes expected. Additionally, with 3D printing, there can be very little waste in the process itself – you are only really printing material where you need it to create a part. Yes, there may be support material required for some overhanging features, but when you compare this to subtractive technologies (e.g. CNC machining), where you start with a solid block of material and subtract what is not required until you’re left with a part, 3D printing can result in much less waste.
Another aspect that holds a lot of potential is in the personalisation aspect – there is growing evidence that if a product has been personalised in some way, for example someone has themselves designed their perfect surf fin and 3D printed it, they are less likely to throw it away compared to a cheap, mass produced product that has less personal value.
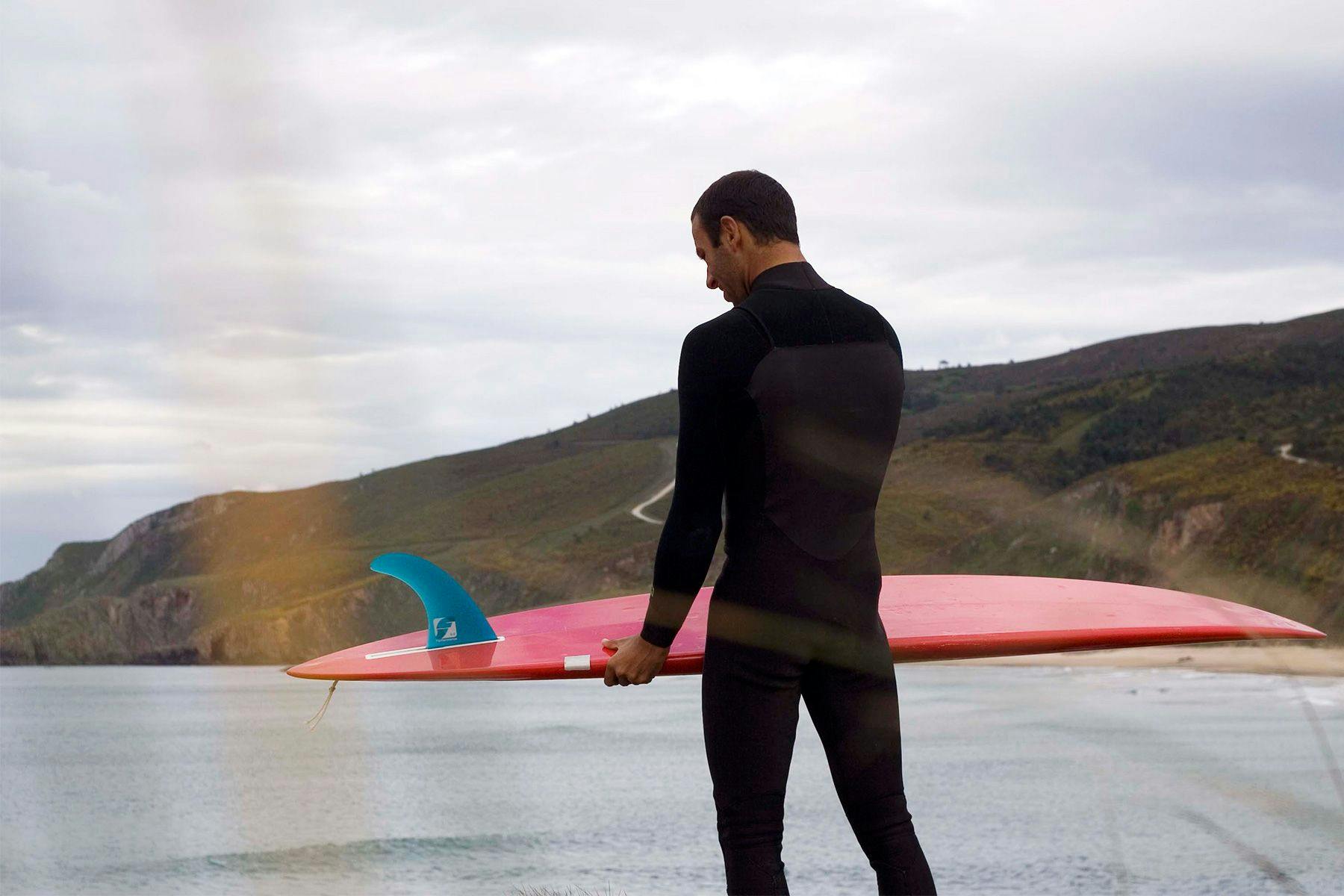
Along those lines, could you please talk a bit about the most popular (as well as the least popular) materials used for printing 3D fins, their upsides and downsides, and what you would like to experiment with next?
PLA is definitely the most popular 3D print material for desktop 3D printers – it is cheap and it is easy to print, and the fumes emitted during printing are quite low. However, one of its weaknesses is that it’s a brittle material, meaning that it can snap quite easily, which is not great for surf fins. A lot of my early fins were 3D printed in another very popular plastic, ABS. This is much more durable and one of the most common plastics found in many of your electronic products, but more difficult to print as it can warp during the transition from hot to cold experienced during printing. More recently I’ve experimented with carbon fibre infused nylon, which is strong and lightweight, but the material requires careful storage as it likes to absorb moisture from the air, and I’ve been printing it on quite an expensive 3D printer that most people wouldn’t own at home.
I think next I’d be interested in experimenting with some recycled filaments. For example, there are some filaments you can buy that have been made from recycled fishing nets, recycled PET bottles and others. Just as 3D printing allows you to experiment with the design, it also allows you to experiment with different materials.
In the paper, you wrote that “the shape of surfboard fins have largely been bio-inspired, assimilating proportions from the dorsal fins of fish and mammals such as the dolphin.” I’m curious to know if you have experimented – or know of someone who has – with other bio-inspired shapes besides the aforementioned? And if not, do you see potential somewhere?
For surf fins, no I’m not aware of any other shapes people are experimenting with that are completely different to the typical fin shapes. The engineering side of me says that these shapes have been optimised using advanced computer simulation software to achieve specific properties in the water, and it is unlikely that a completely new shape will perform better. Evolution has also seen these shapes tested over millions of years! The more creative design side of me wonders whether it still wouldn’t be fun to try some different shapes – perhaps inspired by aircraft like the stealth fighter? Or with textured surfaces, rather than being completely smooth? There is certainly potential to use 3D printing to try different things that manufacturers are unlikely to try.
During this research, you observed closely all aspects of fin design. Was there a particular element – such as fin placement or foil, for instance – that struck you as being generally underestimated or overlooked?
The thing that I realised was how complex such a seemingly simple part was! I initially started this project thinking I’d just need a few simple variables to allow people to create just about any fin shape they wanted, but as I dove into the research, I realised there were many different parts of the fin shape that provide different performance characteristics. I ended up with quite a few different parameters that people can change and interact with in my CAD system, shown below. I probably haven’t surfed long enough or with enough different fins to really understand the practical effects each of these play on performance, but I think many people will be surprised about what sorts of dimensions could be changed and that they may like to experiment with.
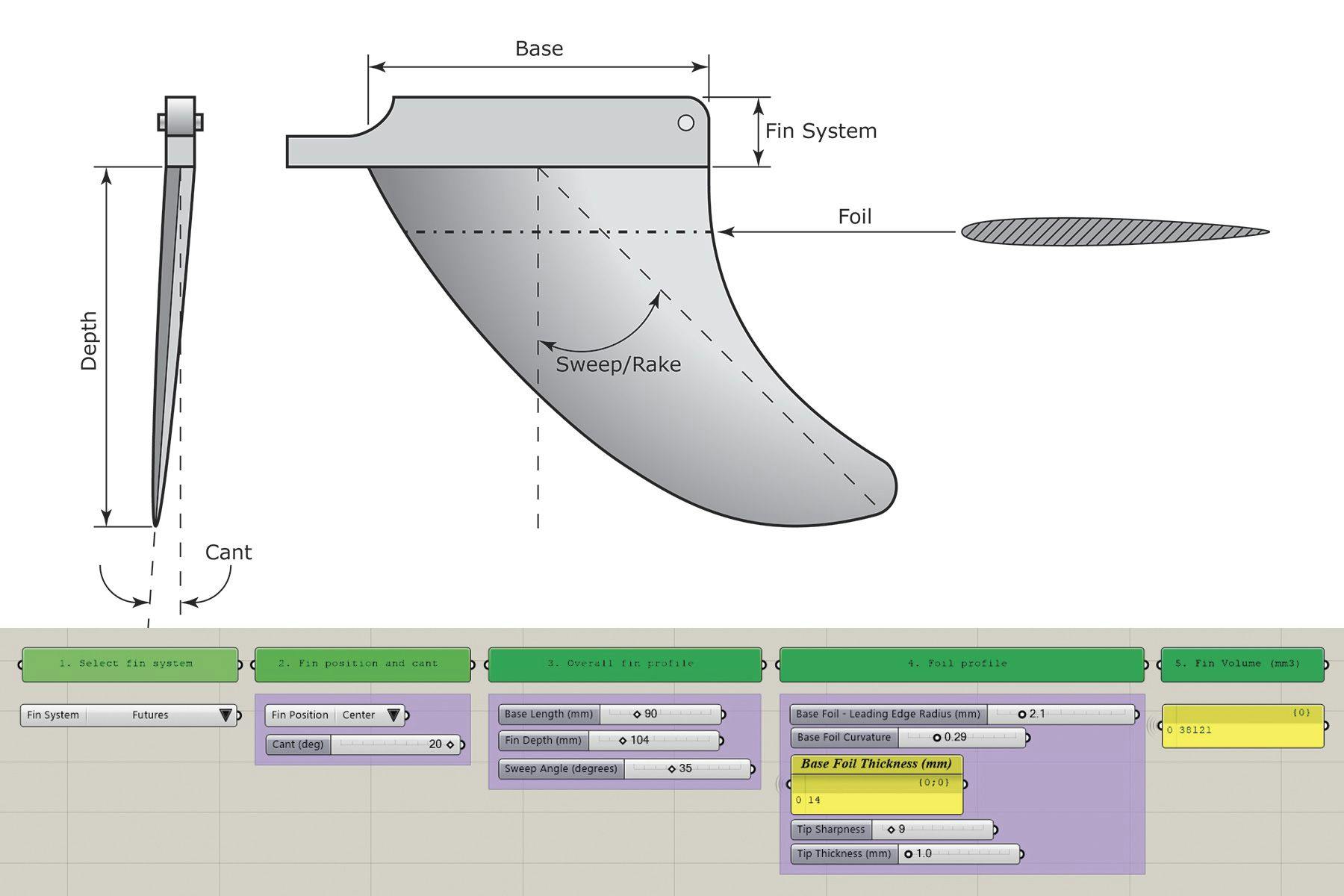
There’s mention in the paper about how some of the previous research on prototyping 3D printed fins showed similar performance to commercially available fins, whilst other studies have presented issues of delamination and weakness around fasteners, for instance. With that in mind, what would you say are the major structural challenges of 3D printed surfboard fins?
Almost all 3D printing processes result in parts that exhibit a property called anisotropy – because of the layer-by-layer nature of 3D printing, there can be an inherent weakness between the 3D printed layers that makes them weak in one orientation, whereas moulded fins have isotropic properties because the material cures as a single solid. It’s a bit like a piece of timber which can be easy to split along the grain, but harder to cut across it. This can be a difficult hurdle to overcome, and may require additional post-processing techniques to improve strength which will add cost to 3D printed fins. The picture below clearly shows the layers in a 3D printed fin using a carbon fibre infused nylon material and specialised 3D printer called the Mark Two, by Markforged. This is one of the most recent surf fins I’ve printed.
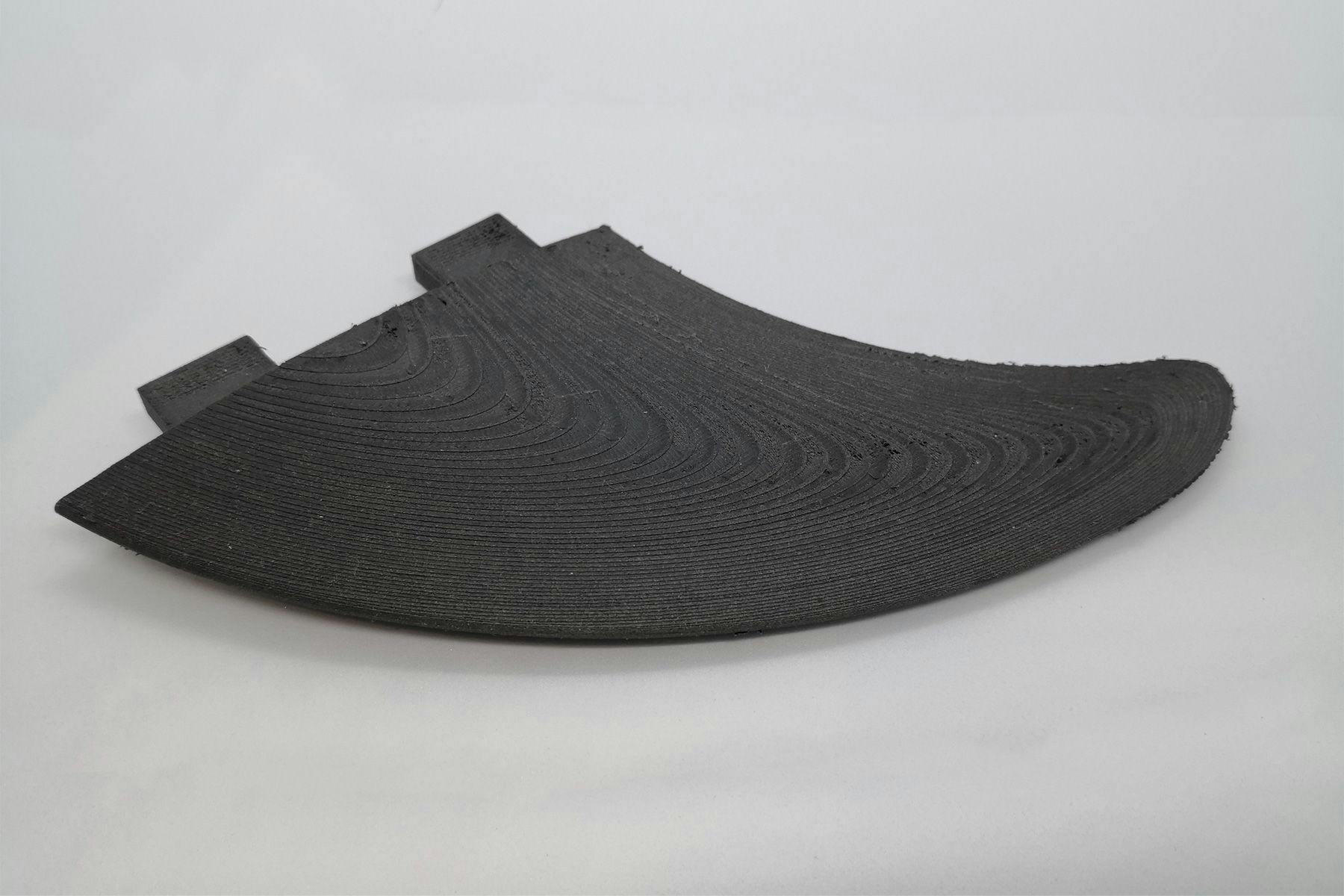
In surfing, more experimentation usually leads to more awareness of one’s surfing skills and equipment, thus providing a better – or at least more holistic – surfing experience. Taking from your blog, I see you love experimenting with design. So I was wondering if, in your opinion, there is a “smart” way of experimenting?
I definitely agree that experimentation leads to more awareness of one’s surfing skills and equipment, or indeed, one’s 3D printing skills and equipment! For me there is a quote that is often discussed in many circles, including design and business – “fail fast and fail often.” This is really possible with 3D printing because you can be out on the water in the morning testing a fin, come back and make some tweaks to the design, set it 3D printing overnight, and be out testing the new fin the next morning. So for me a “smart” way of experimenting is to do just enough to learn what you need to progress to the next step, and iteratively improve a design.
I’m very inspired by James Dyson and his story of the 5,126 “failed” prototype vacuum cleaners before finally perfecting his cyclonic technology. I’m also very happy to share my own failures on my blog, and below is one of my first failed kitesurfing fins which I was able to use for about 15 hours on the water before it broke. The design was quickly improved to be stronger around the screw fixing locations, and lasted much longer. Being comfortable with failure is difficult to learn (especially for my university students who want good marks, not to fail!) but it’s an important part of the learning and experimentation process.
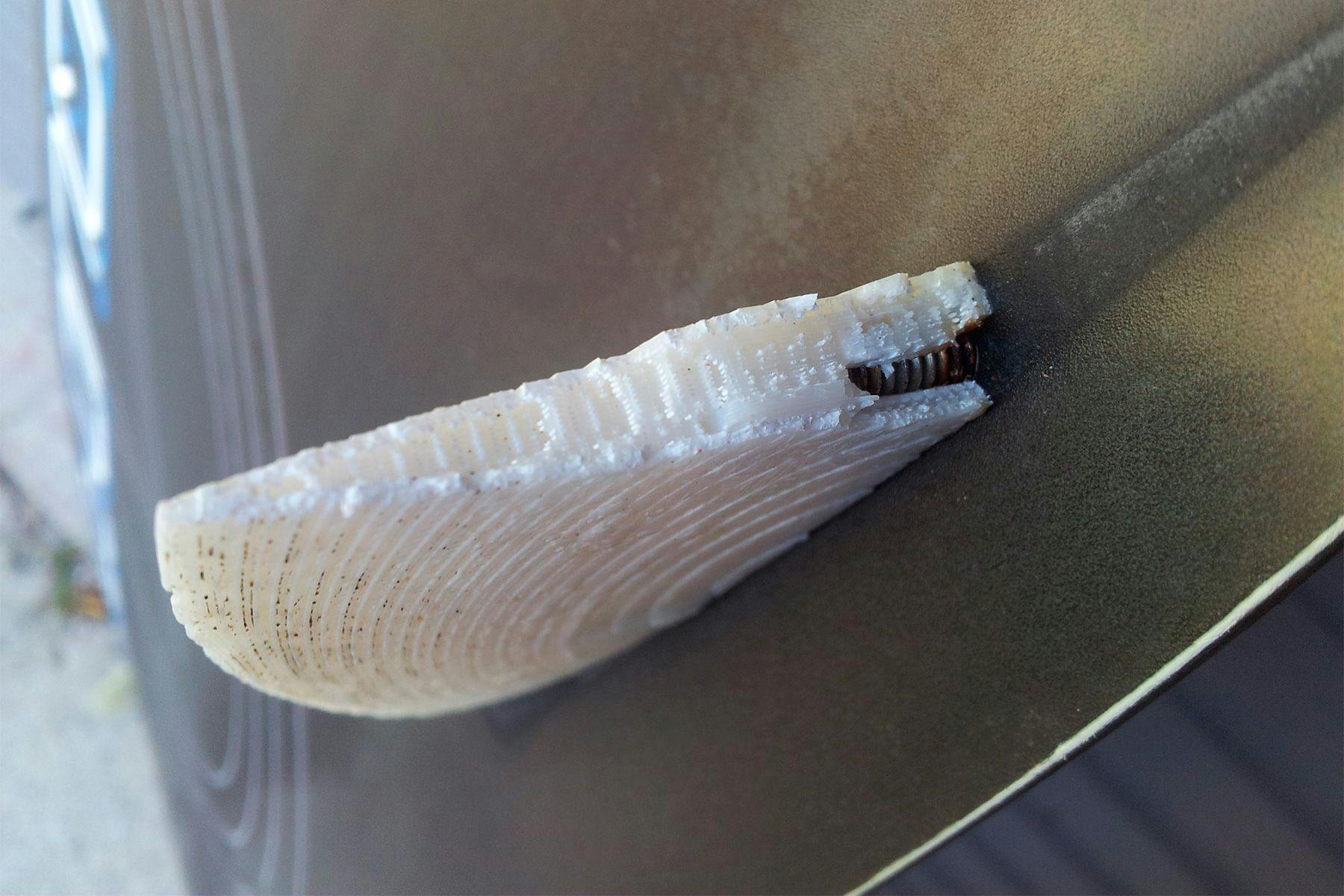
Similarly, in what ways do you reckon experimenting with the creation of their own 3D printed fins could improve a surfer’s performance and surfing experience?
I think this links well with the previous question – through the process of experimentation, you learn more about your equipment and your surfing. You become more attuned to the effects different fins or board shapes have on your experience because you are thinking about the changes you’ve made and assessing the effects. I think most athletes, even recreational, understand how their performance and enjoyment of a sport is tightly linked with the equipment they use, and will experiment with modifications, even if it’s as simple as trying a different insole in a running shoe. It’s quite natural and 3D printing just provides a way to fabricate more advanced types of products to experiment with.
As part of this research, you have successfully tested two prototypes in flatwater ocean paddling conditions, but, as stated in the results, further testing is necessary to understand how such kinds of fins respond under forces experienced in surf conditions. Even so, have you any theories on what to expect in terms of performance, versatility, and durability from a 3D printed fin compared to the existing mass-produced ones?
At the time of writing the paper I had only tested 2 different fins based off my CAD tool, however, I’ve now also experimented with 3D printed carbon fibre surf fins which are very strong and lightweight, with stiffness properties that can be modified through the addition of continuous carbon fibre directly during the 3D print process (pictured previously). Based on the research out of the University of Wollongong, and my years of using 3D printed kitesurfing and SUP fins, I’m very confident that 3D printed fins are not something coming in the future, but something that is already very achievable and will only improve as the technology and materials mature.
We have seen 3D printed surfboards, 3D printed fins… When you think of this surfing-3D-printing combination, what other areas do you think are worth exploring?
In the surfing world there isn’t a lot of equipment required besides the board and fins, so there probably isn’t a lot more scope for 3D printing. I don’t think 3D printing a leg rope or wetsuit is really ideal! One area I’ve experimented with are custom floaty packs for my action camera (pictured below), and a replacement locking mechanism for an adjustable SUP paddle. Peripheral equipment like this for surfers is certainly an opportunity. Otherwise as I’ve described and experienced myself, some of the cousins to surfing, like kitesurfing, windsurfing, SUPing etc. can definitely benefit from similar 3D printed fins and boards, or indeed other equipment that these sports require (harnesses, paddles, etc). I look forward to seeing what people come up with!
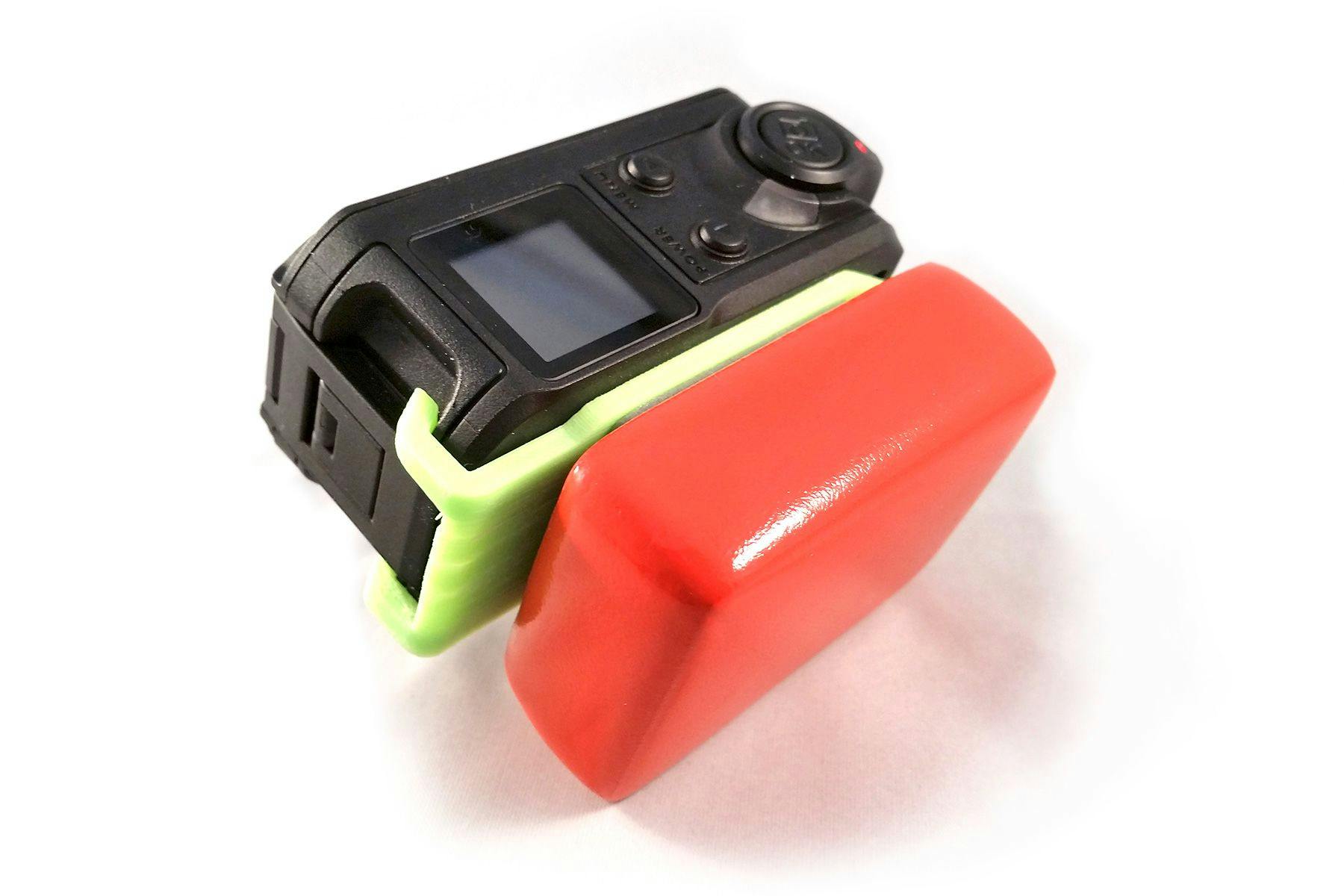
Finally, what are your thoughts on 4D printing, and how do you expect to use it in your future researches and experiments?
4D printing is an interesting research area – basically, the idea that a 3D printed object will change shape based on some sort of stimuli after printing (e.g. heat, moisture, etc). However, it is quite an early and experimental field with limited applications right now. A lot of the more direct or short-term applications are in robotics, but many applications that I’m most interested in are likely in the medical field, which is where I work. Some of these may include scaffolds that are 3D printed and implanted in the body, allowing a patient’s own cells to grow within the scaffold to repair bone, for example, before dissolving away. These are already being utilised in some patients, and we are doing a lot of research into this right now for craniofacial applications. Some of the more “futuristic” types of 4D prints, that may include human organs, are still much further away, although there is a lot of progress every year in this space.
*****
Check out James’ blog for more information on 3D printing or follow him on Instagram to keep up to date with his latest experiments.